Phụ gia sản xuất bao bì nhựa – Bí quyết tạo nên chất lượng
Ngành công nghiệp bao bì nhựa ngày nay không chỉ đơn thuần dừng lại ở việc sản xuất ra những chiếc túi để chứa đựng sản phẩm. Đằng sau một chiếc túi nilon đạt yêu cầu về độ bền, độ trong, màu sắc, khả năng chống dính, độ bóng hay tính phân hủy sinh học… là cả một hệ thống kỹ thuật phức tạp mà trong đó, các chất phụ gia đóng vai trò then chốt. Có thể chia phụ gia thành hai nhóm chính: phụ gia hỗ trợ sản xuất và phụ gia tạo màu sắc, đặc tính đặc biệt cho sản phẩm. Hãy cùng chúng tôi tìm hiểu chi tiết từng nhóm và vai trò của từng loại trong thực tiễn sản xuất bao bì nhựa nhé.
A. Phụ gia hỗ trợ sản xuất bao bì nhựa
Trong quá trình sản xuất bao bì nhựa, các chất phụ gia hỗ trợ đóng vai trò thiết yếu và không thể thay thế, bởi chúng chính là yếu tố đảm bảo cho dây chuyền vận hành ổn định, nguyên liệu chảy đều, màng nhựa không bị dính, kẹt hay phân hủy ở nhiệt độ cao. Nhờ có các chất trợ gia công, chất chống dính, chất trượt, chất ổn định nhiệt và chống oxy hóa…, sản phẩm làm ra mới đạt được độ đồng đều, độ bền cơ học và hiệu suất sản xuất cao. Không có các phụ gia này, quy trình gia công sẽ dễ gặp trục trặc, chất lượng túi không ổn định, thậm chí gây hỏng hóc máy móc và tổn thất nguyên vật liệu. Vì vậy, phụ gia hỗ trợ sản xuất chính là “xương sống” kỹ thuật trong công nghệ tạo ra túi nilon chất lượng cao hiện nay.
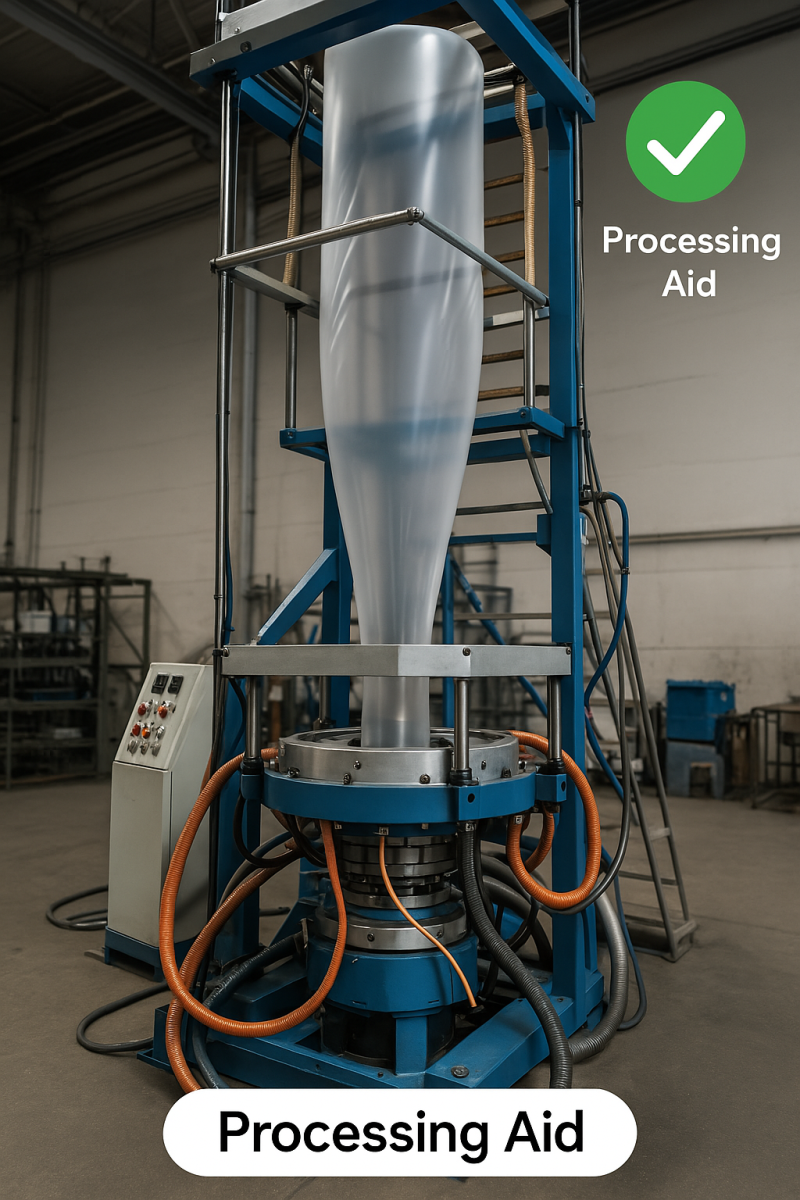
1. Chất trợ gia công (Processing Aid):
Trong lĩnh vực gia công nhựa, đặc biệt là với các loại nhựa có độ nhớt cao như PVC, HDPE, hoặc các dòng nhựa kỹ thuật, việc đảm bảo dòng chảy ổn định và giảm lực cắt trong suốt quá trình ép, đùn, thổi là điều kiện tiên quyết để tạo ra sản phẩm có chất lượng cao. Trong bối cảnh đó, Chất trợ gia công (Processing Aid) chính là thành phần không thể thiếu, giúp tối ưu hóa tính năng xử lý nguyên liệu, tăng tốc độ sản xuất và ổn định hình dáng sản phẩm.
a. Công dụng và tính cần thiết của chất trợ gia công
- Cải thiện độ chảy (melt flow) của nhựa, đặc biệt là trong các hệ nhựa có độ nhớt cao hoặc chứa nhiều phụ gia.
- Giảm áp suất đầu khuôn và lực cắt, từ đó giảm tiêu hao năng lượng, giảm tải cho thiết bị.
- Ổn định dòng chảy nhựa, giúp sản phẩm có biên dạng đồng đều, không bị dao động hoặc biến dạng khi ra khuôn.
- Ngăn hiện tượng gợn sóng, vết xước, vết sọc, cải thiện bề mặt sản phẩm.
- Tăng hiệu suất trộn phụ gia và màu, tạo độ phân tán tốt hơn, đặc biệt khi sản xuất masterbatch.
- Giúp khởi động máy nhanh hơn, dễ vệ sinh đầu đùn, hạn chế đóng cặn trong quá trình vận hành.
Chất trợ gia công là thành phần cực kỳ quan trọng trong sản xuất ống nhựa, tấm nhựa, màng film, chi tiết ép phun và sản phẩm đùn kỹ thuật, đặc biệt là khi sử dụng nhựa tái sinh hoặc công thức nhiều phụ gia khác nhau.
b. Nguyên lý hoạt động
Chất trợ gia công hoạt động theo cơ chế làm giảm độ nhớt và ma sát nội tại trong pha nóng chảy của nhựa. Cụ thể:
- Trong hệ nhựa nhiệt dẻo, phụ gia này hoạt động như một chất làm trơn vi mô giữa các phân tử polymer, giúp các chuỗi dễ dàng trượt lên nhau mà không bị cản trở.
- Trong hệ PVC không hóa dẻo (rigid PVC), chất trợ gia công còn giúp kết dính các hạt polymer lại với nhau trong giai đoạn nóng chảy, tạo cấu trúc đồng nhất và dẻo dai.
- Với hệ thống máy đùn, nó còn giúp làm sạch đầu khuôn và ổn định áp suất đầu ra, đặc biệt khi chạy tốc độ cao hoặc thay đổi nguyên liệu.
c. Thành phần và cấu tạo hóa học
Tùy theo loại nhựa và ứng dụng cụ thể, chất trợ gia công có thể có các cấu trúc hóa học khác nhau:
- Acrylic Processing Aid (APAs):
- Đây là loại phổ biến nhất, là poly(methyl methacrylate) (PMMA) biến tính hoặc copolymer.
- Được thiết kế để tương thích tốt với PVC, cải thiện hiệu suất nóng chảy và độ đánh bóng bề mặt.
- Có nhiều cấp độ trọng lượng phân tử tùy ứng dụng: tốc độ nóng chảy cao, độ bền va đập, hoặc độ bóng cao.
- Fluoropolymer-based Processing Aid:
- Dùng cho nhựa polyolefin (PE, PP), đặc biệt là màng mỏng thổi tốc độ cao.
- Chất này giúp ngăn dính khuôn và tạo màng trơn tại thành khuôn, giảm hiện tượng “melt fracture” (vỡ dòng chảy).
- Thường dùng ở liều rất thấp (200–2000 ppm).
- Polysiloxane-based Additive:
- Dạng nhũ tương hoặc tổ hợp, dùng trong một số ứng dụng đặc biệt với polycarbonate (PC), nylon, TPE.
d. Một số nhãn hiệu và nhà cung cấp nổi bật
- Kaneka (Nhật Bản):
- Dòng KANACRYSTAL, KANAPLUS – chuyên về Processing Aid acrylic dùng cho PVC và nhựa kỹ thuật.
- Arkema (Pháp):
- Sản phẩm Durastrength®, Clearstrength®, Plastistrength® – chất trợ gia công kết hợp tăng độ va đập, độ bền, tính thẩm mỹ cho PVC.
- Rohm and Haas (nay thuộc Dow Chemical, Hoa Kỳ):
- Dòng Paraloid® K-series là hệ Processing Aid nổi tiếng nhất thế giới cho ngành PVC.
- Daikin (Nhật Bản):
- Cung cấp Polyflon™ PPA – hệ fluoropolymer chuyên dùng cho PE/PP trong công nghệ đùn tốc độ cao.
- Shandong Rike (Trung Quốc):
- Một trong những nhà cung cấp lớn về APA tại châu Á, sản phẩm có hiệu quả cao, giá thành cạnh tranh.
2. Phụ gia trơn (Lubricant):
Trong sản xuất nhựa công nghiệp, đặc biệt là các sản phẩm đùn, ép phun, ép đúc hoặc đúc thổi, phụ gia trơn (Lubricant) đóng vai trò cực kỳ quan trọng trong việc cải thiện tính gia công, bảo vệ thiết bị và đảm bảo chất lượng sản phẩm. Dù thường chỉ chiếm một tỷ lệ nhỏ trong công thức phối trộn, nhưng nếu thiếu phụ gia trơn, hiệu suất sản xuất sẽ giảm rõ rệt và nguy cơ hỏng hóc máy móc gia tăng đáng kể. Tùy vào loại nhựa, thiết bị và yêu cầu sản phẩm, việc lựa chọn đúng loại internal lubricant hoặc external lubricant không chỉ tối ưu hóa hiệu suất sản xuất mà còn ảnh hưởng trực tiếp đến chất lượng bề mặt, độ bền và giá trị sử dụng của sản phẩm cuối cùng.
a. Công dụng và tính cần thiết của phụ gia trơn
- Giảm ma sát nội tại giữa nhựa nóng chảy và bề mặt kim loại của thiết bị (trục vít, thành xi lanh, khuôn đúc), từ đó giúp dòng chảy nhựa mượt hơn, ổn định hơn.
- Ngăn chặn hiện tượng dính khuôn, dính trục, hoặc cháy sém khi gia công ở nhiệt độ cao.
- Giảm lực cắt và mô-men xoắn, giúp giảm tiêu thụ năng lượng trong quá trình đùn hoặc ép.
- Kéo dài tuổi thọ thiết bị, giảm hao mòn cơ khí.
- Cải thiện bề mặt sản phẩm, giảm vết sọc, vết xước hoặc bọt khí.
- Tăng tốc độ sản xuất, ổn định chất lượng lô hàng.
Phụ gia trơn đặc biệt cần thiết trong các loại nhựa có độ nhớt cao hoặc khó gia công như PVC, HDPE, PA, PC, ABS, hoặc trong các sản phẩm có biên dạng khuôn phức tạp.
b. Nguyên lý hoạt động
Phụ gia trơn hoạt động dựa trên cơ chế giảm ma sát phân tử, thông qua việc tạo một lớp “phim trơn” mỏng giữa nhựa và bề mặt kim loại của thiết bị. Tùy theo đặc tính phân cực của phụ gia, có hai nhóm chính:
- Phụ gia trơn nội (Internal Lubricant): phân tán đều trong pha nhựa nóng chảy, làm giảm ma sát giữa các phân tử nhựa, từ đó cải thiện dòng chảy và giảm lực cắt. Loại này không ảnh hưởng đến bề mặt sản phẩm.
- Phụ gia trơn ngoại (External Lubricant): tập trung chủ yếu ở bề mặt tiếp xúc giữa nhựa và thiết bị, tạo lớp màng bôi trơn, giúp nhựa không bám vào kim loại. Thường là các chất ít tương thích với nhựa để dễ "tách" ra ngoài.
c. Thành phần và cấu tạo hóa học
Phụ gia trơn có thể có nguồn gốc hữu cơ, vô cơ, hoặc polymer biến tính, với các nhóm chất phổ biến như:
- Axit béo và muối kim loại:
- Stearic acid (C₁₇H₃₅COOH)
- Calcium stearate, Zinc stearate, Magnesium stearate
→ thường dùng cho PVC, PS, ABS.
- Paraffin wax (sáp paraffin):
- Sáp dầu mỏ đã tinh chế, chuỗi C20–C40, thường dùng làm trơn ngoài cho PP, PE.
- Polyethylene wax (PE wax):
- Chuỗi polymer ngắn của polyethylene, dùng cho nhựa kỹ thuật hoặc phối trộn masterbatch.
- Ester phức, amide béo:
- Ví dụ: glycerol monostearate (GMS), behenamide – có hiệu quả cao trong nhựa nhiệt dẻo.
- Silicone-based lubricant:
- Dùng trong sản phẩm yêu cầu độ trơn cực cao, chống dính khuôn tốt, đặc biệt với polycarbonate (PC), nylon.
d. Một số nhãn hiệu và nhà cung cấp nổi tiếng
- Baerlocher (Đức):
- Một trong những tập đoàn hàng đầu thế giới về phụ gia cho nhựa, nổi bật với dòng sản phẩm Baerolub, Baeropan, chuyên dụng cho PVC, PP, PE.
- Clariant (Thụy Sĩ):
- Dòng Licowax, Licocare, Hostalub – phụ gia trơn cao cấp dùng cho nhiều loại nhựa và elastomer.
- Honeywell (Hoa Kỳ):
- Hãng nổi tiếng với AC Polyethylene Waxes, Micronized Wax, phục vụ cả ngành bao bì, ép phun và masterbatch.
- PMC Biogenix (Hoa Kỳ):
- Chuyên về amide béo như Kemamide, Adolube – phụ gia trơn và trượt phổ biến trong ngành thổi màng, ép đùn.
- Fine Organics (Ấn Độ):
- Một trong những nhà sản xuất lớn về ester, GMS, phụ gia dạng hạt sinh học dùng trong ngành thực phẩm, bao bì thân thiện môi trường.
- Shandong Huaxia (Trung Quốc):
- Cung cấp các loại sáp PE, paraffin wax, stearate dùng phổ biến trong ngành nhựa giá rẻ và phổ thông.
3. Chất ổn định nhiệt (Heat Stabilizer):
Trong sản xuất nhựa, đặc biệt là nhựa PVC và một số loại nhựa kỹ thuật có tính nhạy cảm với nhiệt, hiện tượng phân hủy nhiệt là một vấn đề cực kỳ nghiêm trọng. Sự phân hủy này không chỉ làm giảm chất lượng sản phẩm mà còn gây phát thải khí độc hại, ăn mòn thiết bị, thay đổi màu sắc và tính chất cơ lý của nhựa. Chính vì vậy, chất ổn định nhiệt (Heat Stabilizer) là thành phần bắt buộc trong hầu hết các công thức phối trộn nhựa hiện đại, đóng vai trò như một “lá chắn vô hình” chống lại tác hại của nhiệt độ cao trong suốt quá trình gia công và sử dụng.
a. Công dụng và tính cần thiết của chất ổn định nhiệt
- Ngăn chặn quá trình phân hủy nhiệt của nhựa trong quá trình gia công, đặc biệt ở các bước như đùn, ép phun, đúc thổi hoặc cán màng.
- Ổn định màu sắc, ngăn hiện tượng ngả vàng, xám hoặc đen do cháy nhựa khi xử lý ở nhiệt cao.
- Duy trì tính chất cơ học của sản phẩm (độ bền kéo, độ dai, khả năng chống va đập).
- Tăng tuổi thọ sử dụng, giúp sản phẩm nhựa không bị lão hóa nhanh dưới ánh nắng, môi trường khắc nghiệt.
- Hạn chế ăn mòn thiết bị do sản phẩm phân hủy (như HCl trong PVC) gây ra trong quá trình vận hành.
Với nhựa PVC (Polyvinyl Chloride), chất ổn định nhiệt là bắt buộc vì bản thân PVC phân hủy rất nhanh ở nhiệt độ > 180°C nếu không có phụ gia bảo vệ.
b. Nguyên lý hoạt động
Chất ổn định nhiệt hoạt động bằng cách:
- Hấp thụ hoặc trung hòa các gốc tự do và phân tử dễ phân hủy sinh ra trong quá trình gia công, ngăn chặn phản ứng dây chuyền gây phá vỡ cấu trúc phân tử nhựa.
- Kết hợp và trung hòa axit sinh ra, ví dụ như HCl trong quá trình phân hủy PVC – một tác nhân xúc tác mạnh khiến nhựa tiếp tục phân hủy nhanh hơn.
- Tạo liên kết tạm thời với các vị trí hoạt hóa, làm chậm quá trình đứt gãy chuỗi polymer.
- Một số hệ còn tạo thành lớp màng bảo vệ vi mô quanh phân tử polymer khi bị đốt nóng.
c. Thành phần và cấu tạo hóa học
Chất ổn định nhiệt có thể chia thành các nhóm chính dựa theo thành phần hóa học:
Hệ ổn định kim loại (Metal-based Stabilizers)
- Muối chì (Lead Stabilizers): như tribasic lead sulfate (TBLS), dibasic lead stearate – hiệu quả cao, bền, giá rẻ, nhưng đang dần bị loại bỏ do độc tính.
- Muối thiếc (Tin Stabilizers): ví dụ methyltin mercaptide, butyltin stabilizers – có hiệu suất cao, ít màu, dùng trong sản phẩm yêu cầu chất lượng cao, thực phẩm.
- Muối canxi-kẽm (Ca/Zn Stabilizers): thay thế không độc cho chì, hiệu suất ổn định, ít ảnh hưởng màu – là xu hướng chính trong bao bì và sản phẩm nhựa thân thiện môi trường.
- Muối bari-kẽm, strontium-zinc, cadmium-based (nay ít dùng).
Chất ổn định hữu cơ (Organic Stabilizers)
- Phosphite ester: hấp thụ gốc tự do, dùng bổ sung trong hệ polyolefin.
- Hindered Phenol: thường đi kèm với chất chống oxy hóa, bảo vệ lâu dài dưới tác động nhiệt nhẹ.
Chất hỗ trợ ổn định (Co-stabilizers)
- Epoxidized soybean oil (ESBO): dầu đậu nành epoxid hóa – vừa bôi trơn nhẹ, vừa ổn định nhiệt, thường dùng trong nhựa dẻo PVC.
- Polyol, β-diketones, thiols: hỗ trợ các hệ chính, tăng hiệu quả và kéo dài thời gian bền nhiệt.
d. Một số nhãn hiệu và nhà cung cấp nổi bật
- Baerlocher (Đức):
- Hệ Baerostab – ổn định chì, thiếc, canxi-kẽm, nổi tiếng toàn cầu trong ngành PVC.
- Adeka (Nhật Bản):
- Sản phẩm ADK STAB – chuyên về phosphite, phenol ổn định cho polyolefin, PET, EVA…
- Songwon (Hàn Quốc):
- Hệ SONGNOX® và SONGSTAB™ – chất ổn định nhiệt và chống oxy hóa, đáp ứng tiêu chuẩn ROHS/REACH.
- PMC Group (Hoa Kỳ):
- Dòng Thermolite® – chất ổn định thiếc chuyên dụng cho PVC cao cấp.
- Valtris (Hoa Kỳ):
- Một trong những nhà sản xuất lớn về thiếc và hệ Ca/Zn cho ngành bao bì, ống, dây cáp.
- Sun Ace (Singapore/Nhật):
- Sản phẩm SUNSTAB – hệ canxi-kẽm và bari-kẽm cho ngành PVC không chì.
4. Chất chống oxy hóa (Antioxidant):
Trong suốt vòng đời của sản phẩm nhựa – từ giai đoạn gia công ở nhiệt độ cao đến quá trình lưu kho, vận chuyển và sử dụng ngoài trời – hiện tượng oxy hóa xảy ra âm thầm nhưng rất nguy hiểm. Oxy, nhiệt, ánh sáng và các tạp chất kim loại có thể tạo ra các gốc tự do phá hủy cấu trúc polymer, làm nhựa giòn, ngả màu, mất độ bền cơ học. Để ngăn chặn quá trình này, ngành nhựa sử dụng một thành phần vô cùng thiết yếu: Chất chống oxy hóa (Antioxidant) – được ví như “lá phổi hóa học” của mỗi công thức nhựa.
a. Công dụng và tính cần thiết của chất chống oxy hóa
- Ngăn chặn quá trình phân hủy oxy hóa của polymer trong quá trình gia công (nhiệt, ma sát, áp suất).
- Ổn định màu sắc, chống ngả vàng, xám, hoặc mất độ bóng sau thời gian sử dụng.
- Duy trì tính chất cơ học của sản phẩm: độ dẻo, khả năng chịu kéo, chịu va đập.
- Kéo dài tuổi thọ sản phẩm, đặc biệt trong điều kiện tiếp xúc ánh sáng, nhiệt độ và không khí liên tục.
- Bảo vệ các phụ gia nhạy cảm khác, như chất ổn định nhiệt, chất tạo màu, chất chống tia UV.
Đặc biệt trong các dòng nhựa như polyolefin (PE, PP), PS, PA, ABS, TPU, và nhựa tái sinh, chất chống oxy hóa là thành phần không thể thiếu để đảm bảo sản phẩm không bị lão hóa sớm.
b. Nguyên lý hoạt động
Phản ứng oxy hóa trong nhựa thường bắt đầu bằng sự hình thành gốc tự do (free radicals) do nhiệt, ánh sáng hoặc oxy tạo ra. Các gốc này sẽ kích hoạt phản ứng dây chuyền phá vỡ chuỗi polymer. Chất chống oxy hóa hoạt động theo hai cơ chế chính:
- Primary Antioxidants (Chất chống oxy hóa chính):
- Làm nhiệm vụ khử gốc tự do, chủ động ngăn chặn phản ứng chuỗi bằng cách cung cấp một nguyên tử hydro để vô hiệu hóa gốc tự do.
- Ví dụ: Hindered phenols, Amines.
- Secondary Antioxidants (Chất chống oxy hóa phụ):
- Phân hủy các hydroperoxide – sản phẩm trung gian của phản ứng oxy hóa – trước khi chúng tạo ra thêm gốc tự do.
- Ví dụ: Phosphites, Thioesters.
Hai nhóm này thường được dùng kết hợp để tạo hiệu ứng “hiệp lực” (synergy), giúp bảo vệ nhựa toàn diện từ lúc gia công đến lúc sử dụng.
c. Thành phần và cấu tạo hóa học
Các chất chống oxy hóa được sử dụng trong ngành nhựa bao gồm:
Hindered Phenolic Antioxidants (Phenol cản trở)
- Cơ chế khử gốc tự do mạnh, ổn định nhiệt.
- Ví dụ:
- BHT (Butylated Hydroxy Toluene)
- Irganox® 1010, 1076 (Ciba/BASF) – phổ biến nhất thế giới.
- AO-60, AO-80.
Phosphite & Phosphonite Antioxidants
- Ổn định màu, phân hủy hydroperoxide trong giai đoạn gia công.
- Ví dụ:
- Tris(nonylphenyl)phosphite (TNPP)
- Irgafos® 168, Weston® 618 (Addivant).
- ADK STAB 2112, ADK STAB PEP-36 (Adeka).
Thioester Antioxidants
- Tăng cường độ bền lâu dài cho sản phẩm ngoài trời.
- Ví dụ: DSTDP, DLTDP.
Blends (Hệ phối hợp AO)
- Sự phối trộn giữa phenol + phosphite + thioester để tối ưu hiệu năng, ứng dụng đa dạng.
d. Một số nhãn hiệu và nhà cung cấp nổi bật
- BASF/Ciba (Đức/Thụy Sĩ):
- Dòng Irganox®, Irgafos® – chuẩn mực toàn cầu trong chống oxy hóa cho PE, PP, ABS, TPE...
- Adeka (Nhật Bản):
- Dòng ADK STAB – chuyên dùng cho polyolefin, PET, EVA, PVC không chứa kim loại nặng.
- Songwon (Hàn Quốc):
- Dòng SONGNOX® – chất chống oxy hóa đơn và phối hợp, có phiên bản tuân thủ ROHS/REACH.
- SI Group (Hoa Kỳ):
- Sản phẩm WESTON®, NAUGARD®, hệ phosphite và phenol dùng cho nhựa kỹ thuật, cao su, masterbatch.
- Clariant (Thụy Sĩ):
- Dòng Hostanox, Hostavin – chuyên dùng cho nhựa kỹ thuật cao cấp.
5. Phụ gia kết tinh (Nucleating Agent):
Trong các loại nhựa bán tinh thể như polypropylene (PP), polyethylene (PE), polyamide (PA) hay polybutylene terephthalate (PBT), cấu trúc tinh thể của polymer đóng vai trò quyết định đến độ bền cơ học, độ trong suốt, độ cứng và thời gian làm nguội trong quá trình gia công. Để kiểm soát và cải thiện cấu trúc tinh thể ấy, ngành nhựa sử dụng một thành phần phụ gia vô cùng quan trọng: Phụ gia kết tinh (Nucleating Agent) – đóng vai trò như “hạt mầm” giúp định hướng quá trình hình thành tinh thể một cách hiệu quả, đồng đều và nhanh chóng.
a. Công dụng và tính cần thiết của phụ gia kết tinh
- Tăng tốc độ kết tinh của polymer trong quá trình làm nguội, giúp rút ngắn chu kỳ ép phun hoặc ép đùn.
- Tăng độ cứng, độ bền kéo và khả năng chống biến dạng nhiệt của sản phẩm.
- Cải thiện độ trong suốt và độ bóng bề mặt (trong các loại nucleating trong suốt – clarifying nucleating agents).
- Ổn định kích thước sản phẩm, giảm co rút và biến dạng sau khi tạo hình.
- Tăng tính đồng nhất của cấu trúc tinh thể, giúp cải thiện các tính chất cơ học và quang học toàn bộ sản phẩm.
- Hỗ trợ kiểm soát tỷ lệ pha vô định hình và pha tinh thể – rất quan trọng trong các ứng dụng kỹ thuật cao.
Phụ gia kết tinh đặc biệt cần thiết trong sản xuất hộp nhựa PP, màng định hình (thermoforming), chai lọ nhẹ, bao bì chịu nhiệt, linh kiện kỹ thuật và các chi tiết cần độ chính xác cao.
b. Nguyên lý hoạt động
Khi nhựa bán tinh thể nguội sau giai đoạn nóng chảy, các chuỗi polymer sẽ sắp xếp lại và hình thành các vùng kết tinh. Tuy nhiên, nếu không có chất xúc tác, quá trình này sẽ diễn ra chậm và thiếu định hướng.
Phụ gia kết tinh hoạt động như những trung tâm hạt nhân (nucleation centers) – nơi các phân tử polymer dễ dàng bắt đầu quá trình kết tinh. Tùy theo mục đích, phụ gia có thể thúc đẩy:
- Kết tinh α (alpha): dạng tinh thể thông dụng, ổn định, giúp tăng độ cứng và độ bền.
- Kết tinh β (beta): ít phổ biến hơn, cho độ dẻo cao hơn – dùng trong một số sản phẩm đặc biệt.
- Kết tinh rõ (clarity nucleation): kiểm soát sự hình thành tinh thể để giữ lại độ trong cho sản phẩm.
c. Thành phần và cấu tạo hóa học
Phụ gia kết tinh được chia thành hai nhóm lớn:
Phụ gia kết tinh vô cơ (Inorganic Nucleating Agents)
- Tồn tại dưới dạng bột mịn hoặc tinh thể tự nhiên, hoạt động dựa trên cấu trúc bề mặt.
- Ví dụ:
- Talc (Mg₃Si₄O₁₀(OH)₂) – thường dùng trong PP để tăng độ cứng và nhiệt.
- Silica, calcium carbonate, kaolin – hỗ trợ kết tinh, giảm giá thành.
- Sodium benzoate, phosphates, metal salts.
Phụ gia kết tinh hữu cơ (Organic Nucleating Agents)
- Hiệu quả cao, có thể dùng với liều lượng thấp, thường dùng để cải thiện độ trong.
- Ví dụ:
- Sorbitol derivatives (đặc biệt là 1,3:2,4-Di-benzylidene sorbitol – DBS).
- Millad® 3988, NX8000 (clarifying agents) – rất nổi tiếng trong ngành bao bì trong suốt.
Ngoài ra còn có các loại nucleating agents đặc biệt cho kết tinh β hoặc đa hướng.
d. Một số nhãn hiệu và nhà cung cấp nổi bật
- Milliken (Hoa Kỳ):
- Dòng Millad® NX8000, Millad® 3988 – phụ gia kết tinh trong suốt hàng đầu thế giới cho PP, được sử dụng rộng rãi trong bao bì thực phẩm, hộp nhựa, chai lọ.
- Hệ nucleating α hiệu quả cao cho ép phun và ép tấm.
- Clariant (Thụy Sĩ):
- Dòng Hydrocerol®, AddWorks® N – phụ gia kết tinh và tạo bọt nhẹ, dùng trong sản phẩm kỹ thuật và bao bì nhẹ.
- Adeka (Nhật Bản):
- Dòng ADK NA-11, NA-21 – nucleating β cho PP và PBT, cải thiện độ dẻo, giảm trọng lượng sản phẩm.
- PolyOne / Avient (Hoa Kỳ):
- Cung cấp hệ masterbatch chứa nucleating agent phối hợp với màu hoặc phụ gia chống trượt, tăng hiệu quả đồng thời.
- GCH Technology (Trung Quốc):
- Nhà sản xuất nucleating giá hợp lý cho thị trường phổ thông, đáp ứng nhiều loại nhựa.
6. Phụ gia khử nước (Desiccant):
Trong quá trình gia công nhựa, đặc biệt là nhựa tái sinh, nhựa hút ẩm cao như PA, PET, PC hoặc nhựa đã tồn kho lâu ngày, độ ẩm tồn dư trong nguyên liệu luôn là một trong những “kẻ thù thầm lặng” gây ra hàng loạt vấn đề nghiêm trọng: bọt khí, lỗ rỗ, cháy sém, giảm độ bền cơ học và ảnh hưởng đến độ bóng, độ trong sản phẩm. Để giải quyết triệt để vấn đề này mà không cần sấy khô bằng nhiệt tốn thời gian, ngành nhựa đã sử dụng một giải pháp rất hiệu quả: Phụ gia khử nước (Desiccant) – hay còn gọi là chất hút ẩm nội bộ trong nhựa.
a. Công dụng và tính cần thiết của phụ gia khử nước
- Hấp thụ trực tiếp lượng nước tự do hoặc liên kết trong nguyên liệu nhựa, xử lý độ ẩm ngay trong quá trình gia công mà không cần sấy sơ bộ.
- Ngăn hiện tượng bọt khí, rỗ tổ ong, lỗ hổng trong sản phẩm – đặc biệt ở các sản phẩm ép phun, đùn màng, đùn ống.
- Cải thiện bề mặt sản phẩm, tăng độ bóng, độ đặc khít, độ trong và tính thẩm mỹ.
- Tăng cường tính ổn định vật lý và cơ học, giúp sản phẩm có độ bền kéo, uốn, va đập tốt hơn.
- Rút ngắn thời gian chuẩn bị nguyên liệu, tiết kiệm năng lượng, đặc biệt hữu ích với nhựa tái chế không ổn định về độ ẩm.
Phụ gia khử nước được xem như giải pháp sấy khô nội bộ, đơn giản – hiệu quả – tiết kiệm, cực kỳ quan trọng trong các ngành sử dụng PP tái sinh, PE, ABS, PA, PET, PC, nhựa màu và masterbatch.
b. Nguyên lý hoạt động
Phụ gia khử nước hoạt động theo cơ chế phản ứng hóa học hoặc hấp phụ vật lý với phân tử nước có trong hỗn hợp nhựa nóng chảy.
Có hai cơ chế chính:
- Cơ chế hóa học (chemical reaction):
- Các hợp chất như canxi oxit (CaO), magie oxit (MgO) phản ứng với nước tạo thành hydroxide, giúp “bắt giữ” nước ngay trong quá trình nóng chảy:
CaO+H2O→Ca(OH)2\text{CaO} + \text{H}_2\text{O} \rightarrow \text{Ca(OH)}_2CaO+H2O→Ca(OH)2
-
- Phản ứng này không tạo khí, không gây bọt – thích hợp cho sản phẩm yêu cầu bề mặt đẹp.
- Cơ chế hấp phụ vật lý (physical adsorption):
- Các vật liệu như silica gel, zeolite hút ẩm nhờ cấu trúc vi mao quản, giữ nước trong lỗ xốp.
Tùy vào yêu cầu sản xuất, loại nhựa và mức độ ẩm, có thể chọn loại phụ gia phù hợp với cơ chế phản ứng nhanh hoặc hút ẩm từ từ.
c. Thành phần và cấu tạo hóa học
Một số chất hoạt động phổ biến trong phụ gia khử nước:
- Canxi oxit (CaO) – dạng siêu mịn, hoạt hóa nhanh, thường được kết hợp với sáp mang để phân tán tốt.
- Magie oxit (MgO) – ít phản ứng hơn CaO, dùng trong hệ polymer nhạy với kiềm.
- Silica gel (SiO₂·nH₂O) – khả năng hút ẩm cao, không phản ứng hóa học.
- Zeolite (aluminosilicate) – có cấu trúc mao quản, hiệu quả trong PET, PA.
- Hợp chất hữu cơ hấp thụ nước – như polyacrylic acid hoặc dẫn xuất cellulose dùng trong nhựa thực phẩm.
Phụ gia thường được chế biến dưới dạng masterbatch chứa 10–50% chất khử ẩm, dễ phối trộn với hạt nhựa nguyên sinh hoặc tái sinh.
d. Một số nhãn hiệu và nhà cung cấp nổi bật
- SUQIAN QINGXIN (Trung Quốc):
- Dòng QX-01, QX-06 – masterbatch khử ẩm gốc CaO chuyên cho nhựa PE, PP tái sinh.
- GCH Technology (Trung Quốc):
- Chuyên sản xuất desiccant masterbatch cho ngành nhựa tái chế, có thể dùng cho thổi màng, ép phun, đùn ống.
- Polyvel (Hoa Kỳ):
- Dòng DMB series – khử nước cho PET, PC, PA với khả năng xử lý ẩm cao, không ảnh hưởng màu.
- GreenTech Additives (Ấn Độ):
- Cung cấp phụ gia hút ẩm thân thiện môi trường, không tạo cặn kiềm, thích hợp cho sản phẩm thực phẩm.
- Ming Chemical (Trung Quốc):
- Sản phẩm MC Desiccant MB có khả năng hấp thụ tới 20% trọng lượng nước so với chính nó.
7. Chất phân tán nhựa (Dispersing Agent):
Trong ngành công nghiệp nhựa, việc trộn lẫn các thành phần như hạt màu (masterbatch), chất độn, chất tạo đặc tính, phụ gia kỹ thuật… vào nền nhựa là một công đoạn bắt buộc để tạo ra sản phẩm có tính năng và hình thức như mong muốn. Tuy nhiên, nếu các thành phần này không được phân tán đều, sản phẩm sẽ gặp hiện tượng loang màu, vón cục, xuất hiện điểm yếu cơ học hoặc rối loạn trong quá trình đùn – ép. Để giải quyết vấn đề này, ngành nhựa sử dụng một phụ gia đóng vai trò vô cùng quan trọng: Chất phân tán nhựa (Dispersing Agent) – hay còn gọi là chất hỗ trợ phân tán.
a. Công dụng và tính cần thiết của chất phân tán nhựa
- Giúp phân tán đồng đều hạt màu, chất độn, chất tạo tính năng vào nền nhựa, đặc biệt trong sản xuất masterbatch, compound và hạt màu.
- Ngăn ngừa hiện tượng vón cục, kết tụ hoặc không đồng nhất, nhất là với các hệ thống chứa bột mịn như CaCO₃, TiO₂, talc, hạt màu hữu cơ.
- Cải thiện độ bền cơ học, độ bóng và độ trong của sản phẩm bằng cách loại bỏ các điểm yếu phân tử do kết tụ hạt.
- Tăng khả năng chảy và hiệu suất gia công, giúp hỗn hợp nhựa – phụ gia đi qua trục vít, khuôn ép một cách trơn tru và ổn định.
- Nâng cao chất lượng phối trộn trong quá trình tạo hạt (pelletizing), tránh phân lớp trong quá trình tạo sợi hoặc đùn màng.
Chất phân tán là thành phần bắt buộc trong sản xuất masterbatch, hạt màu, compound nhựa kỹ thuật và cả các ứng dụng có phụ gia vô cơ/hữu cơ liều cao.
b. Nguyên lý hoạt động
Chất phân tán hoạt động theo cơ chế:
- Giảm năng lượng bề mặt của hạt chất rắn (bột màu, bột độn), từ đó dễ dàng phá vỡ các kết tụ và phân bố đều trong nền polymer.
- Tạo màng bảo vệ mỏng quanh hạt, ngăn không cho chúng kết tụ trở lại (hiện tượng “re-agglomeration”).
- Một số chất phân tán có khả năng gắn kết với cả nền nhựa và phụ gia, làm cầu nối trung gian (interface modifier), từ đó tăng tương thích giữa các pha khác nhau.
c. Thành phần và cấu tạo hóa học
Tùy thuộc vào loại nhựa nền và phụ gia cần phân tán, chất phân tán có thể có thành phần rất đa dạng:
- Ester của axit béo:
- Glycerol monostearate (GMS), sorbitan ester – phổ biến trong masterbatch nhựa PE, PP.
- Waxes (Sáp):
- PE wax, PP wax, amide wax – giảm ma sát, tăng phân tán và cải thiện độ bóng.
- Copolymer gốc acrylic, maleic anhydride, EVA:
- Dùng trong hệ thống phối hợp với hạt màu hữu cơ, chất độn vô cơ mịn.
- Silane coupling agent:
- Giúp tăng tương thích giữa phụ gia vô cơ (như silica, talc) với nền nhựa.
- Phụ gia phân tán chuyên dụng:
- Dạng polymer có đầu phân cực – không phân cực, hỗ trợ phân tán đa chức năng trong hệ masterbatch kỹ thuật.
d. Một số nhãn hiệu và nhà cung cấp nổi bật
- BYK (Đức):
- Dòng BYK-P, BYK-W – chuyên về dispersing cho pigment, filler, masterbatch kỹ thuật cao.
- Clariant (Thụy Sĩ):
- Dòng Licowax, Licocare, dispersing wax giúp cải thiện phân tán và bề mặt sản phẩm.
- Polyvel (Hoa Kỳ):
- Dòng D-Series – polymer dispersant cho PE/PP masterbatch chứa chất độn cao.
- Fine Organics (Ấn Độ):
- Dòng Finawax – ester phân tán cho ứng dụng pigment, filler và cải thiện độ bóng.
- Croda Polymer Additives (Anh):
- Các dispersing agent gốc tự nhiên, thân thiện môi trường, dùng cho bao bì thực phẩm và y tế.
8. Phụ gia tách khuôn (Mold Release):
Trong các quy trình ép phun, ép đùn, đúc nén hay ép thổi nhựa, việc sản phẩm sau khi định hình bị dính chặt vào khuôn là một hiện tượng phổ biến và gây ra nhiều hệ lụy: khó tháo sản phẩm, trầy xước bề mặt, sai kích thước, gãy vỡ khi lấy ra, làm chậm chu kỳ sản xuất và gia tăng tỷ lệ lỗi. Để khắc phục tình trạng này, ngành nhựa sử dụng một phụ gia chuyên biệt: Phụ gia tách khuôn (Mold Release Agent) – một trong những trợ thủ đắc lực giúp bảo vệ bề mặt khuôn, giảm lực ma sát và đảm bảo tính toàn vẹn của sản phẩm.
a. Công dụng và tính cần thiết của phụ gia tách khuôn
- Giúp sản phẩm dễ dàng tách khỏi khuôn sau khi định hình, không bị dính chặt hoặc biến dạng khi tháo khuôn.
- Bảo vệ bề mặt khuôn khỏi trầy xước, bám nhựa hoặc bị ăn mòn, kéo dài tuổi thọ khuôn và giảm chi phí bảo trì.
- Cải thiện bề mặt sản phẩm, giúp bề mặt mịn hơn, đồng đều hơn, tránh vết xước do va chạm hoặc bóc tách cưỡng bức.
- Giảm thời gian làm sạch khuôn, tăng số lần chu kỳ sản xuất trước khi cần bảo trì.
- Tăng tốc độ sản xuất và giảm tỷ lệ lỗi do sản phẩm kẹt trong khuôn hoặc bị vỡ khi tháo ra.
Phụ gia tách khuôn đặc biệt cần thiết trong sản xuất nhựa kỹ thuật (PC, POM, PA, ABS), linh kiện điện tử, chi tiết chính xác, vật liệu nhiệt rắn và cả các sản phẩm composite (nhựa gia cường sợi thủy tinh).
b. Nguyên lý hoạt động
Phụ gia tách khuôn hoạt động theo hai nguyên lý chính:
- Tạo một lớp màng mỏng có tính năng chống dính giữa bề mặt khuôn và sản phẩm nhựa. Lớp màng này có khả năng chịu nhiệt và chống ma sát cao, ngăn không cho nhựa bám vào kim loại.
- Giảm năng lượng bề mặt của khuôn, khiến nhựa không thể kết dính hoàn toàn và dễ dàng trượt ra khi khuôn mở.
Tùy theo ứng dụng và yêu cầu sản xuất, phụ gia tách khuôn có thể là loại pha trộn nội bộ trong nhựa (internal mold release) hoặc dạng xịt/lỏng bôi trơn lên khuôn (external mold release).
c. Thành phần và cấu tạo hóa học
Phụ gia tách khuôn được phân loại theo thành phần hóa học chính:
Silicone-based (gốc silicon)
- Hiệu quả cao, bền nhiệt, chống dính tốt.
- Phù hợp với hầu hết các loại nhựa, đặc biệt là ABS, PC, PA.
- Tuy nhiên có thể ảnh hưởng đến khả năng in ấn hoặc sơn phủ sau đó (do bề mặt quá trơn).
Waxes (sáp)
- PE wax, ester wax, carnauba wax.
- Dễ sử dụng, giá thành thấp, tương thích tốt với nhiều hệ polymer.
- Thường dùng cho ép phun, ép đùn PVC, PE, PP.
Fluoropolymer-based
- Siêu chống dính, chịu nhiệt cực cao.
- Dùng cho nhựa nhiệt rắn, nhựa kỹ thuật, composite.
Non-silicone organic release
- Dùng khi cần sơn hoặc in sau khi tháo khuôn.
- Không để lại dư lượng cản trở xử lý bề mặt.
Metal soap
- Kẽm stearate, canxi stearate – có thể phối hợp làm phụ gia trơn kiêm tách khuôn nội bộ.
d. Một số nhãn hiệu và nhà cung cấp nổi bật
- Chem-Trend (Hoa Kỳ):
- Dòng Mono-Coat®, Chemlease® – mold release chuyên dùng cho composite, cao su và ép phun kỹ thuật.
- Wacker (Đức):
- Dòng Silres® – silicone release agent cao cấp dùng cho nhiệt dẻo và nhiệt rắn.
- Henkel (Đức):
- Dòng Loctite® Frekote® – nổi tiếng trong ngành khuôn epoxy, polyester, polyurethane.
- Axel Plastics (Hoa Kỳ):
- Dòng MoldWiz® – phụ gia tách khuôn nội và ngoại cho nhựa nhiệt dẻo và đúc sợi thủy tinh.
- Shandong Sanrun Additives (Trung Quốc):
- Nhà sản xuất wax tách khuôn cho PVC, PE, masterbatch giá hợp lý, phổ biến tại châu Á.
Trong thực tế sản xuất hiện đại, đa phần các phụ gia hỗ trợ sản xuất như chất trợ gia công, chất ổn định nhiệt, chất chống oxy hóa, chất chống dính, chất trượt, phụ gia khử nước… đã được tích hợp sẵn vào hạt nhựa nguyên sinh hoặc masterbatch bởi các nhà sản xuất nguyên liệu lớn. Nhờ đó, các doanh nghiệp sản xuất bao bì và sản phẩm nhựa không còn phải can thiệp sâu vào khâu phối trộn từng thành phần kỹ thuật riêng lẻ như trước. Những hạt nhựa "thiết kế theo công năng" (functionalized resins) hiện nay thường đã được tinh chỉnh theo từng nhu cầu cụ thể: dễ gia công, chống bám khuôn, chống vàng, bền nhiệt, kéo dài tuổi thọ thiết bị… tùy theo mục tiêu sử dụng.
Chính vì vậy, việc quá lo lắng về các phụ gia kỹ thuật hỗ trợ sản xuất không còn là ưu tiên hàng đầu, mà đã được chuyển giao cho các hãng nguyên liệu và nhà cung cấp compound chuyên nghiệp. Thay vào đó, vấn đề quan trọng hơn mà các nhà sản xuất bao bì cần thực sự nắm vững là nhóm phụ gia tạo đặc tính sản phẩm – như hạt màu, chất làm trong, chất tăng độ bóng, chất phân tán, phụ gia kết tinh, chất tạo hương, phụ gia diệt khuẩn, chất chống UV hay phụ gia phân hủy sinh học… Đây mới chính là những yếu tố ảnh hưởng trực tiếp đến chất lượng cảm quan, tính năng sử dụng, thẩm mỹ, độ an toàn và giá trị thị trường của sản phẩm.
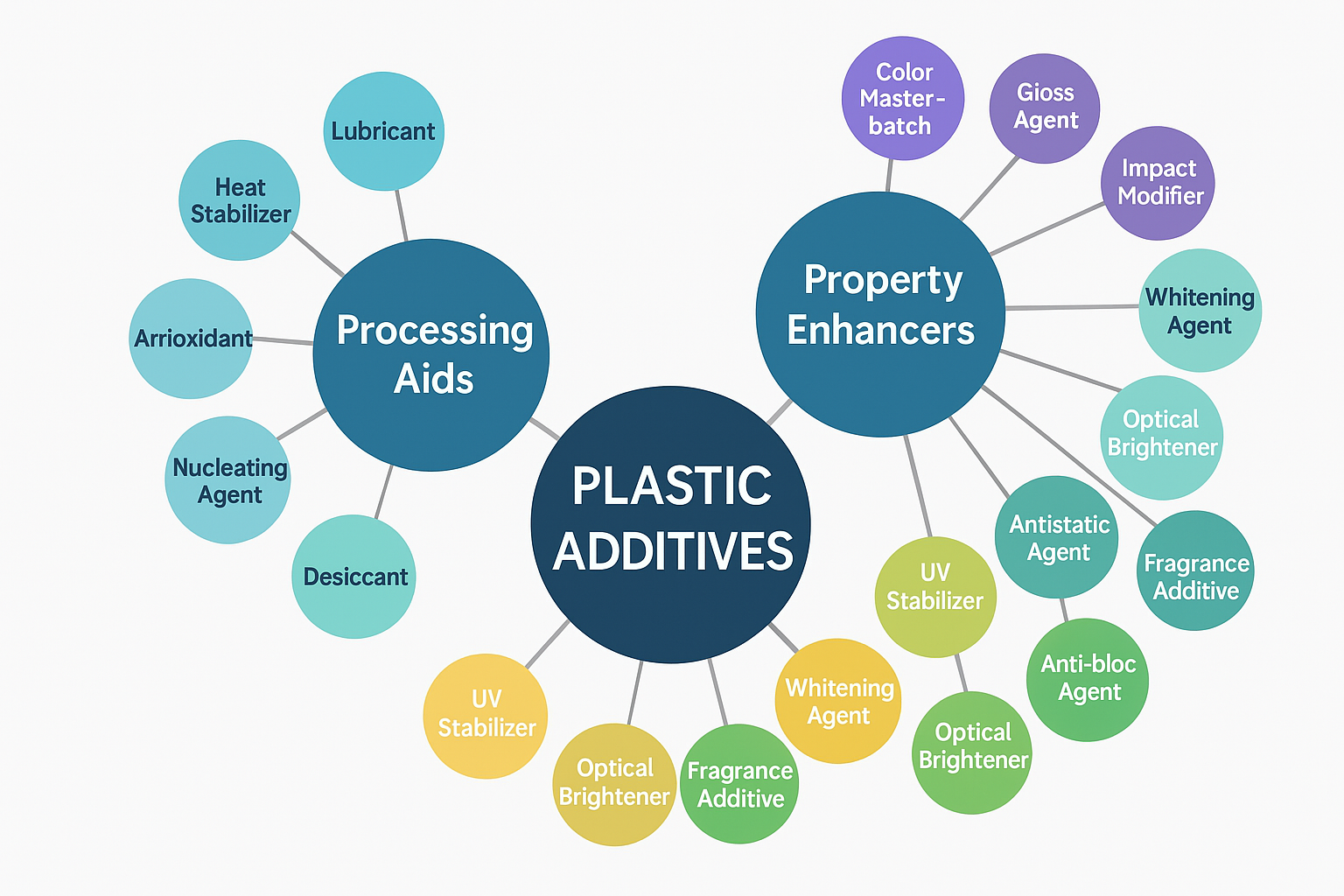
B. Phụ gia tạo màu sắc và đặc tính sản phẩm
Phụ gia tạo màu sắc và đặc tính sản phẩm không chỉ là yếu tố bổ sung mà chính là linh hồn của sản phẩm nhựa, quyết định toàn bộ cảm quan, chức năng và giá trị sử dụng. Trong khi các phụ gia kỹ thuật hỗ trợ quá trình sản xuất vận hành trơn tru, thì chính nhóm phụ gia tạo đặc tính mới là yếu tố định hình sản phẩm trong mắt người tiêu dùng: một chiếc túi trong veo, bóng sáng hay mờ nhám cao cấp, một bao bì dẻo dai hay giòn dễ rách, có thơm dịu hay có khả năng kháng khuẩn – tất cả đều đến từ lựa chọn và phối hợp đúng các phụ gia này.
Chúng không chỉ mang lại sự khác biệt về ngoại hình, mà còn là công cụ kỹ thuật để nâng cao độ bền, độ an toàn, khả năng tương thích môi trường, và hiệu quả bảo quản sản phẩm. Trong bối cảnh cạnh tranh khốc liệt hiện nay, nơi khách hàng ngày càng nhạy cảm với từng chi tiết, thì khả năng làm chủ các phụ gia tạo màu và đặc tính chính là lợi thế cạnh tranh cốt lõi của nhà sản xuất. Nó không chỉ giúp tạo ra sản phẩm “đẹp mắt” mà còn “thông minh” và “tốt hơn” – một cách âm thầm nhưng mạnh mẽ để xây dựng thương hiệu bền vững.
Hiểu rõ các phụ gia tạo đặc tính không chỉ giúp tối ưu hóa công thức phối trộn theo mục tiêu (trong – mờ, bóng – mịn, dai – cứng, thơm – diệt khuẩn…) mà còn giúp doanh nghiệp nâng tầm thiết kế, linh hoạt cải tiến sản phẩm và phản ứng nhanh với nhu cầu thị trường ngày càng đa dạng và khắt khe. Trong thời đại bao bì không còn chỉ là vật chứa mà là công cụ truyền thông và tạo trải nghiệm người dùng, sự am hiểu sâu sắc về các phụ gia tạo đặc tính chính là năng lực cốt lõi của nhà sản xuất bao bì chuyên nghiệp.
1. Hạt màu (Color Masterbatch):
Trong sản xuất nhựa hiện đại, màu sắc không chỉ là yếu tố trang trí, mà còn là ngôn ngữ thương hiệu, công cụ phân loại sản phẩm và đôi khi là chỉ dẫn chức năng. Để tạo ra màu sắc đồng nhất, ổn định và dễ kiểm soát trong quá trình gia công, ngành nhựa sử dụng một giải pháp thông minh: Hạt màu (Color Masterbatch) – một dạng phụ gia đậm đặc chứa sắc tố, được thiết kế sẵn để pha loãng vào nhựa nền theo tỷ lệ mong muốn.
a. Công dụng và tính cần thiết của hạt màu
- Tạo màu sắc đồng đều, sắc nét, bền màu cho sản phẩm nhựa.
- Dễ phối trộn, dễ kiểm soát tỉ lệ màu, không gây bụi như màu bột, an toàn cho người vận hành.
- Tăng tính thẩm mỹ và bản sắc thương hiệu, giúp bao bì nổi bật, dễ nhận diện và hấp dẫn thị trường.
- Ổn định trong quá trình gia công, không làm thay đổi đặc tính cơ học của sản phẩm nếu sử dụng đúng loại nhựa nền tương thích.
- Tích hợp được các chức năng khác như chống UV, chống tĩnh điện, tăng bóng, hoặc hiệu ứng đặc biệt (ánh kim, ánh ngọc, phát quang...).
Hạt màu là phụ gia không thể thiếu trong tất cả các sản phẩm nhựa, từ bao bì, đồ gia dụng, phụ kiện kỹ thuật, đến chi tiết công nghiệp, điện tử, ô tô.
b. Nguyên lý hoạt động
Hạt màu hoạt động như một tổ hợp màu sắc dạng hạt rắn, trong đó:
- Sắc tố màu (pigment hoặc dye) được phân tán đều trong một loại nhựa nền tương thích (PE, PP, PS, PET, ABS...).
- Một lượng chất phân tán và chất trợ gia công được bổ sung để đảm bảo màu phân bố đều khi gia công ở nhiệt độ cao.
- Khi được trộn với nhựa nguyên sinh, hạt màu hòa tan hoặc phân tán hoàn toàn vào nền nhựa, cho ra màu sắc cuối cùng đúng như thiết kế.
c. Thành phần và cấu tạo hóa học
Thành phần chính của hạt màu bao gồm:
- Pigment hoặc Dye (Chất màu):
- Có thể là vô cơ (Titanium Dioxide, Carbon Black, Iron Oxide…) – độ bền cao, giá rẻ, màu đậm.
- Hoặc hữu cơ (Azo, Phthalocyanine…) – cho màu tươi, rực rỡ, phổ màu rộng hơn.
- Nhựa nền (Carrier Resin):
- Thường cùng loại với nhựa thành phẩm: PE, PP, PS, EVA, PET, ABS, PC…
- Giúp hạt màu tương thích, không gây phân lớp hoặc ảnh hưởng tính chất cơ học.
- Chất phân tán (Dispersing Agent):
- GMS, ester wax, EVA… giúp màu phân bố đều, không vón cục.
- Phụ gia hỗ trợ (tùy chọn):
- Chất chống tia UV, chất tăng bóng, chất ổn định nhiệt…
d. Một số nhãn hiệu và nhà cung cấp nổi bật
- Ampacet (Hoa Kỳ):
- Một trong những nhà sản xuất hạt màu lớn nhất thế giới, với dải sản phẩm bao phủ cả ngành bao bì, ô tô, điện tử.
- Clariant (Thụy Sĩ):
- Dòng Renol®, CESA® – nổi bật với độ bền màu, màu an toàn thực phẩm và hạt màu chống UV.
- Cabot (Hoa Kỳ):
- Chuyên cung cấp Carbon Black Masterbatch, dùng trong ống, màng đen, chi tiết kỹ thuật.
- PolyOne / Avient (Hoa Kỳ):
- Cung cấp hạt màu tùy chỉnh cho ứng dụng cao cấp: phát sáng, chuyển màu, ánh kim.
- Plastiblends (Ấn Độ):
- Nhà sản xuất hạt màu giá hợp lý, được dùng phổ biến tại châu Á, trong bao bì mềm và màng mỏng.
- Sơn Hải, Việt Ý, Dana Masterbatch (Việt Nam):
- Các nhà sản xuất hạt màu nội địa với năng lực tùy biến theo đơn đặt hàng, chất lượng ngày càng cạnh tranh quốc tế.
2. Chất làm mờ (Anti-glare Agent):
Trong ngành bao bì và vật liệu nhựa, không phải lúc nào độ bóng cũng là yếu tố được ưu tiên. Trong nhiều ứng dụng – đặc biệt là bao bì mỹ phẩm, dược phẩm, bao bì cao cấp hoặc chi tiết nhựa có yêu cầu thẩm mỹ tinh tế – bề mặt mờ nhẹ, không bóng lóa lại được đánh giá cao nhờ khả năng giảm phản chiếu, tăng chiều sâu thị giác và tạo cảm giác sang trọng. Để tạo nên hiệu ứng này, ngành nhựa sử dụng Chất làm mờ (Anti-glare Agent) – một loại phụ gia quan trọng giúp kiểm soát mức độ khuếch tán ánh sáng trên bề mặt sản phẩm.
a. Công dụng và tính cần thiết của chất làm mờ
- Tạo hiệu ứng mờ (matte finish) trên bề mặt màng nhựa, tấm nhựa hoặc sản phẩm ép phun.
- Giảm độ bóng gương (gloss level), hạn chế hiện tượng phản xạ ánh sáng gay gắt (anti-glare), đặc biệt dưới đèn hoặc ánh sáng tự nhiên.
- Tăng chiều sâu và tính thẩm mỹ cao cấp cho bao bì mỹ phẩm, dược phẩm, sản phẩm chăm sóc cá nhân.
- Giúp sản phẩm không in dấu vân tay, không trơn trượt, thuận tiện cho thao tác.
- Tạo độ đồng đều cho bề mặt khi dùng màu pastel, ánh ngọc hoặc hiệu ứng bán trong suốt.
Chất làm mờ là phụ gia không thể thiếu trong sản phẩm đòi hỏi thẩm mỹ tinh tế, nơi mà độ bóng quá cao có thể làm giảm giá trị cảm quan hoặc ảnh hưởng đến trải nghiệm người dùng.
b. Nguyên lý hoạt động
Chất làm mờ hoạt động dựa trên hai cơ chế chính:
- Tán xạ ánh sáng: các hạt phụ gia siêu mịn phân bố đều trong nhựa tạo ra sự gồ ghề vi mô trên bề mặt, khiến ánh sáng chiếu tới bị phân tán thay vì phản xạ đều – từ đó tạo cảm giác mờ, giảm bóng.
- Khác biệt chiết suất: chất làm mờ có chiết suất khác với nhựa nền, dẫn đến hiện tượng lệch pha ánh sáng – tăng hiệu ứng mờ mà không làm thay đổi màu sắc.
Mức độ mờ phụ thuộc vào kích thước hạt, chiết suất và nồng độ phụ gia được sử dụng.
c. Thành phần và cấu tạo hóa học
Các chất làm mờ thông dụng bao gồm:
- Silica siêu mịn (Amorphous Silica):
- Phổ biến nhất, có khả năng tán xạ cao, không màu, bền nhiệt, không ảnh hưởng cơ lý.
- Kích thước hạt thường từ 1–6 micron.
- Waxes đặc biệt (PE wax, PP wax):
- Tạo bề mặt mịn, mềm mại, dùng cho màng thổi, màng ép nhiều lớp.
- Polyolefin Terpolymer:
- Hiệu ứng mờ nhẹ, dùng trong màng mềm, màng co nhiệt.
- PMMA hoặc Acrylic beads:
- Tạo bề mặt nhám trong tấm nhựa cao cấp, thích hợp cho in UV hoặc sơn phủ sau đó.
- Siloxane hoặc các hạt polymer tán xạ:
- Dùng trong hệ nhựa kỹ thuật như PC, PMMA, PS – cho hiệu ứng mờ rất ổn định.
d. Một số nhãn hiệu và nhà cung cấp nổi bật
- W.R. Grace (Hoa Kỳ):
- Dòng Syloid® – silica mờ nổi tiếng toàn cầu, dùng cho màng PE, PP, PET.
- Evonik (Đức):
- Dòng Aerosil®, ACEMATT® – silica hoạt hóa cao, dùng cho nhựa và sơn phủ.
- Tosoh (Nhật Bản):
- Dòng CEINFO® – silica xử lý bề mặt, tạo mờ mà vẫn giữ độ trong suốt.
- Deuchem (Đài Loan):
- Dòng Matting Agent dùng trong film BOPP, màng ép nhũ và túi mỹ phẩm cao cấp.
- Clariant (Thụy Sĩ):
- Dòng Licowax® – wax làm mờ nhẹ, dùng trong bao bì mềm và nhựa kỹ thuật.
3. Chất tăng độ bóng (Gloss Agent):
Trong ngành bao bì nhựa, đặc biệt là bao bì quà tặng, mỹ phẩm, sản phẩm tiêu dùng cao cấp hay màng trang trí, bề mặt sáng bóng, sắc nét, có chiều sâu ánh sáng luôn là yếu tố thu hút thị giác mạnh mẽ và tạo cảm giác cao cấp cho sản phẩm. Để đạt được hiệu ứng này, ngoài việc kiểm soát quy trình gia công và lựa chọn nguyên liệu nhựa phù hợp, nhà sản xuất cần đến một trợ thủ đắc lực: Chất tăng độ bóng (Gloss Agent) – loại phụ gia giúp tối ưu hóa độ phản xạ ánh sáng và tạo lớp phủ sáng rõ trên bề mặt sản phẩm nhựa.
a. Công dụng và tính cần thiết của chất tăng độ bóng
- Tăng độ bóng bề mặt, giúp sản phẩm trở nên nổi bật, sáng rõ, phản chiếu tốt ánh sáng môi trường.
- Cải thiện cảm quan và độ hấp dẫn thị giác, đặc biệt với bao bì quà tặng, túi gói hoa, bao bì mỹ phẩm và sản phẩm tiêu dùng cao cấp.
- Tăng khả năng in ấn, ép nhũ và cán màng, tạo độ sắc nét cho hình ảnh hoặc văn bản in trên sản phẩm.
- Làm đầy các lỗ vi mô trên bề mặt nhựa, giúp bề mặt mịn hơn và phản xạ ánh sáng đồng đều hơn.
- Cải thiện khả năng chảy và định hình màng nhựa, hỗ trợ đùn/thổi ở tốc độ cao.
Chất tăng độ bóng đặc biệt hữu dụng trong màng PP, BOPP, màng PET, màng ép nhũ, túi trong suốt, hộp nhựa và bao bì sản phẩm quà tặng.
b. Nguyên lý hoạt động
Chất tăng độ bóng hoạt động theo hai nguyên lý chính:
- Làm đầy bề mặt: các hạt vi mô (wax, polymer hoặc silica biến tính) lấp đầy các lỗ nhỏ và vết sần siêu nhỏ trên bề mặt nhựa, tạo bề mặt mịn tuyệt đối.
- Tăng khả năng phản xạ ánh sáng: bằng cách làm đồng nhất độ chiết quang trên bề mặt, giúp ánh sáng phản xạ tuyến tính thay vì bị phân tán – tạo hiệu ứng bóng gương.
Một số chất còn hoạt động như màng phủ nội bộ trong quá trình tạo hình, giúp giảm ma sát và tăng hiệu ứng sáng bóng tự nhiên.
c. Thành phần và cấu tạo hóa học
Các chất tăng độ bóng phổ biến hiện nay bao gồm:
- Polyethylene wax (PE wax):
- Tạo bề mặt mịn, sáng rõ, tương thích tốt với PE, PP, PS.
- Có thể dùng riêng hoặc phối hợp với chất làm trong.
- Amide wax:
- Như erucamide, oleamide – có khả năng tăng độ bóng và hỗ trợ tách khuôn.
- Polymethyl methacrylate (PMMA) microbeads:
- Tạo độ bóng cao cấp, thường dùng trong tấm nhựa, film PET hoặc ứng dụng in UV.
- Organosilicone compounds:
- Có khả năng tự sắp xếp bề mặt khi nóng chảy, tạo lớp phản xạ ánh sáng mạnh.
- Tổ hợp wax – ester – chất hoạt động bề mặt:
- Dùng trong masterbatch tăng bóng, vừa dễ phân tán, vừa cải thiện dòng chảy.
d. Một số nhãn hiệu và nhà cung cấp nổi bật
- Clariant (Thụy Sĩ):
- Dòng Licowax®, Hostanox® – wax tăng bóng và ổn định bề mặt trong masterbatch kỹ thuật.
- Evonik (Đức):
- Dòng ACEMATT®, TEGOMER® – tăng bóng kèm kiểm soát ma sát, dùng cho film và màng co.
- Lubrizol (Hoa Kỳ):
- Dòng Lanco® Wax – tạo hiệu ứng bóng cao, phù hợp cho PET, PC, nhựa in ấn.
- BYK (Đức):
- Dòng BYK-W – phụ gia tăng bóng cho cả nhựa và mực in UV, acrylic.
- Fine Organics (Ấn Độ):
- Dòng Finawax® – wax sinh học, giúp tăng bóng và tăng phân tán trong masterbatch màu.
4. Chất làm trong (Clarifying Agent):
Trong ngành bao bì và sản phẩm nhựa tiêu dùng, độ trong suốt không chỉ là yếu tố kỹ thuật mà còn là biểu tượng của sự tinh khiết, cao cấp và chuyên nghiệp. Một sản phẩm nhựa càng trong, càng sắc nét thì càng dễ dàng thu hút thị giác và truyền tải trọn vẹn nội dung bên trong. Tuy nhiên, nhiều loại nhựa bán tinh thể như polypropylene (PP) hoặc polyethylene (PE) khi nguội sẽ tự nhiên kết tinh thành các hạt nhỏ, gây mờ đục. Để khắc phục điều này, ngành nhựa sử dụng Chất làm trong (Clarifying Agent) – một loại phụ gia đặc biệt có khả năng kiểm soát cấu trúc tinh thể để tăng độ trong suốt mà không ảnh hưởng đến cơ tính của sản phẩm.
a. Công dụng và tính cần thiết của chất làm trong
- Tăng độ trong suốt, giúp sản phẩm nhựa trở nên rõ nét, sáng hơn và truyền ánh sáng tốt hơn.
- Cải thiện độ bóng bề mặt, tạo cảm giác sắc sảo, cao cấp và tinh tế.
- Tăng giá trị cảm quan cho các sản phẩm như hộp thực phẩm, bao bì mỹ phẩm, chai lọ trong suốt, màng gói hoa, túi quà…
- Rút ngắn chu kỳ làm nguội, tăng hiệu suất sản xuất do thúc đẩy quá trình kết tinh vi mô đồng đều.
- Không ảnh hưởng đáng kể đến độ bền cơ học, thậm chí một số loại còn cải thiện độ cứng và ổn định nhiệt.
Chất làm trong là phụ gia không thể thiếu trong sản xuất PP, PP random copolymer, màng BOPP, bao bì trong suốt và các sản phẩm nhựa gia dụng cao cấp.
b. Nguyên lý hoạt động
Khi polymer bán tinh thể như PP nguội sau quá trình đùn hoặc ép phun, nó hình thành các cấu trúc tinh thể spherulite. Nếu các spherulite này lớn, chúng tán xạ ánh sáng và khiến sản phẩm bị mờ.
Chất làm trong hoạt động như một tác nhân tạo mầm kết tinh (nucleating agent đặc biệt), giúp hình thành các tinh thể cực nhỏ và đồng đều – nhờ đó giảm hiện tượng tán xạ ánh sáng, làm sản phẩm trở nên trong suốt hơn.
Một số chất còn có khả năng điều chỉnh mật độ và tốc độ hình thành tinh thể, giúp tối ưu cả độ trong và độ bền cơ học.
c. Thành phần và cấu tạo hóa học
Chất làm trong chủ yếu thuộc nhóm phụ gia hữu cơ, hoạt động ở nồng độ rất thấp (0.1–0.3%) nhưng hiệu quả cao. Các nhóm phổ biến:
- Sorbitol và dẫn xuất:
- Đặc biệt là 1,3:2,4-di(benzylidene)sorbitol (DBS) – loại phổ biến nhất.
- Hiệu quả cao, giá thành hợp lý, dùng nhiều trong hộp PP, màng BOPP.
- MDBS (methylated DBS):
- Hiệu suất cao hơn, ít ảnh hưởng đến mùi, phù hợp bao bì thực phẩm.
- Ví dụ: Millad® NX8000 – chuẩn mực toàn cầu.
- Clarifying polymer additives:
- Hệ polymer tương thích giúp kiểm soát vi mô bề mặt, dùng cho PET, PS.
- Silica biến tính hoặc nano-filler đặc biệt:
- Tăng độ trong suốt trong các loại nhựa blend hoặc nhựa có pha phụ gia cao.
d. Một số nhãn hiệu và nhà cung cấp nổi bật
- Milliken (Hoa Kỳ):
- Dòng Millad® 3988, NX8000 – chất làm trong cho PP nổi bật nhất thế giới, tương thích với cả PP homo và copolymer.
- NX8000 được chứng nhận FDA và EU cho tiếp xúc thực phẩm.
- Clariant (Thụy Sĩ):
- Dòng AddWorks® N – clarifying agent kết hợp tính năng nucleating và tăng bề mặt.
- ADEKA (Nhật Bản):
- Dòng ADK NA-11, NA-21 – chất làm trong và tạo cấu trúc β tinh thể đặc biệt.
- PolyOne / Avient (Hoa Kỳ):
- Cung cấp masterbatch chứa clarifying agent cho sản phẩm bao bì kỹ thuật cao.
- Shandong Rainwell (Trung Quốc):
- Nhà cung cấp phụ gia làm trong giá hợp lý, được sử dụng trong bao bì phổ thông tại châu Á.
5. Chất tăng độ dai (Impact Modifier):
Trong các ứng dụng yêu cầu sản phẩm nhựa có khả năng chịu lực cao, không giòn vỡ, không nứt khi bị va đập – đặc biệt trong môi trường lạnh hoặc khi sản phẩm mỏng nhẹ – việc chỉ dùng nhựa nguyên sinh là chưa đủ. Nhiều loại polymer như PVC, PS, ABS, PMMA, PC, PP vốn có độ cứng cao nhưng lại giòn, dễ gãy. Để khắc phục điểm yếu này mà không làm mất đi độ bền, ngành nhựa sử dụng Chất tăng độ dai (Impact Modifier) – phụ gia giúp hấp thụ năng lượng va đập, làm mềm dẻo cấu trúc polymer và tăng khả năng chống gãy nứt.
a. Công dụng và tính cần thiết của chất tăng độ dai
- Tăng khả năng chịu va đập, giảm hiện tượng nứt, gãy, vỡ khi có tác động cơ học mạnh.
- Cải thiện độ bền dai trong môi trường nhiệt độ thấp, nơi nhựa thường trở nên giòn hơn.
- Ổn định hình dáng và kích thước sản phẩm, tránh hiện tượng nứt ứng suất trong thời gian dài sử dụng.
- Duy trì độ cứng và bề mặt ổn định, nếu dùng đúng liều lượng và loại phù hợp với polymer nền.
- Tăng độ linh hoạt của sản phẩm nhựa, thích hợp với các chi tiết kỹ thuật, thiết bị điện, ống nước, linh kiện ô tô, đồ gia dụng…
Đây là phụ gia không thể thiếu trong các sản phẩm nhựa kỹ thuật, nhựa chống va đập, nhựa định hình mỏng, bao bì công nghiệp và vật liệu nhựa tái sinh cần tăng độ bền.
b. Nguyên lý hoạt động
Chất tăng độ dai hoạt động dựa trên cơ chế:
- Phân tán trong nền nhựa dưới dạng các hạt đàn hồi (rubber-like domains) có khả năng hấp thụ và phân tán năng lượng va đập.
- Khi bị tác động, năng lượng không tập trung tại một điểm gây nứt gãy, mà được lan truyền qua các hạt modifier – từ đó giảm ứng suất tập trung và ngăn cản vết nứt phát triển.
- Một số loại còn tương thích hóa với nền polymer, giúp duy trì độ bóng, độ trong hoặc không làm giảm tính cơ học nền.
c. Thành phần và cấu tạo hóa học
Tùy theo loại nhựa và yêu cầu sản phẩm, các chất tăng độ dai phổ biến bao gồm:
- Acrylic-based modifiers (AIM):
- Tăng độ dai cho PVC cứng (uPVC), không làm giảm độ trong suốt.
- Dùng trong ống nước, tấm nhựa, sản phẩm trong nhà.
- MBS (Methyl methacrylate-Butadiene-Styrene):
- Tăng độ dẻo cho PVC mà vẫn giữ độ trong, phù hợp với màng mỏng, chai lọ, sản phẩm gia dụng.
- CPE (Chlorinated Polyethylene):
- Tăng độ dai cho PVC, PE, thường dùng trong sản phẩm cần chống va đập cao: ống công nghiệp, cửa nhựa.
- EPDM, POE (Polyolefin elastomer):
- Dùng cho PP, PE, HIPS, tăng dẻo dai cho chi tiết ô tô, điện tử.
- ABS powder, EVA-based modifiers:
- Dùng cho nhựa PS, PC/ABS blend, tạo dẻo dai cho sản phẩm cứng.
- CORE-SHELL modifiers:
- Cấu trúc hạt 2 lớp (lõi mềm – vỏ cứng), tăng va đập mà không ảnh hưởng bề mặt và độ bóng.
d. Một số nhãn hiệu và nhà cung cấp nổi bật
- Kaneka (Nhật Bản):
- Dòng Kane Ace®, Acrylic Modifier KM Series – tăng độ dai cho PVC, PC, PMMA.
- LG Chem (Hàn Quốc):
- Chuyên cung cấp POE, EPDM cho ứng dụng PP/PE chịu va đập cao.
- Dow Chemical (Hoa Kỳ):
- Dòng Engage®, Fusabond® – modifier cho polyolefin và các blend nhựa kỹ thuật.
- Arkema (Pháp):
- Sản phẩm Durastrength® – chất tăng độ dai cao cấp cho PVC và hợp chất blend.
- Shandong Rike (Trung Quốc):
- Cung cấp modifier giá cạnh tranh, dùng cho tấm, ống và nhựa định hình.
6. Chất chống tĩnh điện (Antistatic Agent):
Tĩnh điện là hiện tượng vật lý thường xuyên xuất hiện trong quá trình sản xuất, đóng gói và sử dụng sản phẩm nhựa, đặc biệt ở các loại nhựa cách điện tốt như PE, PP, PS hoặc PET. Khi bề mặt nhựa cọ xát hoặc tiếp xúc với dòng khí khô, nó dễ tích tụ điện tích âm – gây ra hàng loạt hệ lụy: hút bụi, bám bẩn, mất thẩm mỹ, phóng tia điện khi chạm vào, hoặc thậm chí làm hỏng linh kiện điện tử nhạy cảm. Để kiểm soát hiện tượng này, ngành nhựa sử dụng Chất chống tĩnh điện (Antistatic Agent) – phụ gia chuyên dụng giúp trung hòa điện tích và ngăn tích lũy tĩnh điện trên bề mặt sản phẩm.
a. Công dụng và tính cần thiết của chất chống tĩnh điện
- Ngăn tích tụ điện tích âm trên bề mặt nhựa, giúp sản phẩm không còn hiện tượng phóng điện khi tiếp xúc.
- Giảm hút bụi, bám bẩn, giúp sản phẩm luôn sạch sẽ, sáng rõ, đặc biệt quan trọng với bao bì trong suốt, tấm hiển thị, hộp linh kiện…
- Bảo vệ linh kiện điện tử, chống nhiễu và hư hỏng do tĩnh điện phát sinh.
- Tăng an toàn sản xuất, tránh cháy nổ do phóng điện trong môi trường có hơi gas hoặc bụi mịn.
- Cải thiện trải nghiệm người dùng, giúp sản phẩm không “giật tĩnh điện” khi sử dụng.
Chất chống tĩnh điện đặc biệt quan trọng trong ngành điện – điện tử, bao bì thực phẩm, dược phẩm, tấm chắn trong suốt, thiết bị văn phòng và bao bì công nghiệp có yêu cầu sạch bề mặt cao.
b. Nguyên lý hoạt động
Chất chống tĩnh điện hoạt động theo hai cơ chế chính:
- Tạo lớp dẫn điện vi mô trên bề mặt sản phẩm, giúp điện tích thoát ra môi trường xung quanh (dẫn điện yếu, không gây sốc).
- Hấp thụ độ ẩm từ không khí, tạo lớp màng dẫn điện mỏng tự nhiên để trung hòa điện tích phát sinh do ma sát.
Tùy vào loại và vị trí sử dụng, chất chống tĩnh điện có thể là:
- Antistatic nội (Internal Antistat): trộn vào nhựa từ đầu, hoạt động trong quá trình gia công và dần di chuyển lên bề mặt.
- Antistatic ngoại (External Antistat): dạng xịt, phủ bề mặt sau khi sản xuất – hiệu quả nhanh, dùng cho tấm, film, màng lớn.
c. Thành phần và cấu tạo hóa học
Một số nhóm chất chống tĩnh điện phổ biến:
- Amin hoặc amide alkyl ethoxylate:
- Gốc phân cực giúp hút ẩm, tạo màng dẫn điện – phổ biến trong PE, PP, PS.
- Ví dụ: ethoxylated fatty amines, quaternary ammonium compounds.
- Polyether hoặc polyester ion hóa:
- Dẫn điện yếu nhưng ổn định – dùng cho nhựa kỹ thuật và môi trường sạch.
- Glycerol monoester, sorbitan ester:
- Vừa là chất chống tĩnh điện vừa giúp phân tán tốt các chất khác trong hệ polymer.
- Carbon black dẫn điện (Conductive Carbon Black):
- Tạo nền dẫn điện vĩnh viễn – dùng trong sản phẩm bảo vệ ESD hoặc linh kiện điện tử.
- Conductive polymer hoặc blend ESD:
- Hệ polymer pha đặc biệt có khả năng dẫn điện ổn định, dùng cho ứng dụng chuyên biệt.
d. Một số nhãn hiệu và nhà cung cấp nổi bật
- Clariant (Thụy Sĩ):
- Dòng AddWorks® ASC, antistatic agent cho bao bì thực phẩm, điện tử, film BOPP.
- Ampacet (Hoa Kỳ):
- Masterbatch chống tĩnh điện dùng cho PP, PE, PET – có phiên bản ESD cho điện tử.
- Sanyo Chemical (Nhật Bản):
- Dòng PELESTAT®, PELECTRON® – phụ gia ESD vĩnh viễn, chuyên cho bao bì điện tử và phòng sạch.
- Fine Organics (Ấn Độ):
- Dòng Finastat® – antistatic thân thiện môi trường, dùng cho nhựa tiêu dùng.
- Shandong Joyforce (Trung Quốc):
- Masterbatch chống tĩnh điện nội bộ giá hợp lý, dùng trong bao bì công nghiệp.
7. Chất chống tia UV (UV Stabilizer):
Khi sản phẩm nhựa được sử dụng ngoài trời hoặc tiếp xúc thường xuyên với ánh nắng, tia cực tím (UV) trong ánh sáng mặt trời chính là “kẻ thù vô hình” gây ra hiện tượng lão hóa nhựa: ngả màu, mất độ bóng, giòn gãy, nứt bề mặt, giảm độ bền và tính thẩm mỹ. Dù không thể nhìn thấy bằng mắt thường, nhưng tia UV có khả năng phá vỡ liên kết phân tử polymer chỉ sau một thời gian ngắn. Để ngăn chặn quá trình phân hủy này, ngành nhựa sử dụng Chất chống tia UV (UV Stabilizer) – một loại phụ gia đặc biệt giúp bảo vệ cấu trúc polymer khỏi tác động của ánh sáng mặt trời, kéo dài tuổi thọ và giữ vững chất lượng sản phẩm.
a. Công dụng và tính cần thiết của chất chống tia UV
- Ngăn ngừa hiện tượng lão hóa do ánh nắng, giữ độ bền cơ học, màu sắc và độ bóng bề mặt.
- Hạn chế ngả vàng, nứt nẻ, vỡ giòn hoặc phấn hóa bề mặt sau thời gian dài sử dụng ngoài trời.
- Tăng tuổi thọ sản phẩm nhựa ngoài trời, đặc biệt trong ngành xây dựng, nông nghiệp, bao bì, đồ dùng sân vườn và linh kiện kỹ thuật.
- Bảo vệ các phụ gia màu, chất tạo trong, chất làm bóng… khỏi bị phân hủy bởi UV.
- Giúp sản phẩm duy trì tính thẩm mỹ và độ an toàn sử dụng theo thời gian.
Chất chống UV là thành phần bắt buộc trong sản phẩm nhựa sử dụng ngoài trời như: màng nhà kính, tấm lấy sáng, dây cáp, linh kiện ô tô, vỏ thiết bị điện tử, thùng nhựa, ghế nhựa, bao bì có yêu cầu trưng bày lâu dài.
b. Nguyên lý hoạt động
Chất chống tia UV hoạt động theo hai cơ chế chính:
- Hấp thụ tia cực tím (UV Absorbers):
- Hấp thụ bức xạ UV và chuyển hóa thành nhiệt năng vô hại, ngăn tia UV phá hủy polymer.
- Phổ biến nhất là benzotriazole, benzophenone, oxanilide, triazine.
- Ổn định gốc tự do (HALS – Hindered Amine Light Stabilizers):
- Trung hòa các gốc tự do được hình thành do tác động của UV, ngăn chặn phản ứng dây chuyền phân hủy polymer.
- Hiệu quả dài hạn, đặc biệt là trong môi trường khắc nghiệt.
Hai loại này thường được sử dụng kết hợp để tăng hiệu quả bảo vệ và mở rộng thời gian hoạt động ngoài trời.
c. Thành phần và cấu tạo hóa học
Một số nhóm chất UV stabilizer chính:
- UV Absorbers:
- Benzotriazole: hoạt động mạnh trong vùng 290–350nm, dùng cho PS, PET, PC.
- Benzophenone: giá thành rẻ, hiệu quả vừa phải.
- Triazine: thế hệ mới, hiệu suất cao, tương thích với nhiều polymer.
- Oxanilide: dùng cho PVC, có khả năng kết hợp màu tốt.
- HALS (Hindered Amine Light Stabilizers):
- Cấu trúc amine bão hòa, có khả năng tái tạo lại sau khi trung hòa gốc tự do.
- Hoạt động bền bỉ, thường dùng trong PE, PP, PU, PA.
- Blend UV + HALS:
- Phối hợp cả hấp thụ và ổn định, tối ưu hóa hiệu quả trong môi trường ngoài trời dài hạn.
d. Một số nhãn hiệu và nhà cung cấp nổi bật
- BASF (Đức):
- Dòng Tinuvin®, Chimassorb® – tiêu chuẩn toàn cầu trong chống UV, dùng cho PE, PP, PC, PVC, PET…
- ADEKA (Nhật Bản):
- Dòng ADK STAB LA Series – UV absorber và HALS thế hệ mới, tương thích cao, hiệu quả lâu dài.
- Songwon (Hàn Quốc):
- Dòng SONGSORB®, SONGNOX® – giải pháp chống UV cho bao bì, film, màng nhà kính và nhựa kỹ thuật.
- Clariant (Thụy Sĩ):
- Dòng Hostavin®, AddWorks® – bảo vệ màu sắc và hiệu ứng bề mặt trong ngành bao bì cao cấp.
- Ampacet (Hoa Kỳ):
- Masterbatch UV dùng cho màng PE, PP, PET, có thể tích hợp cùng hạt màu.
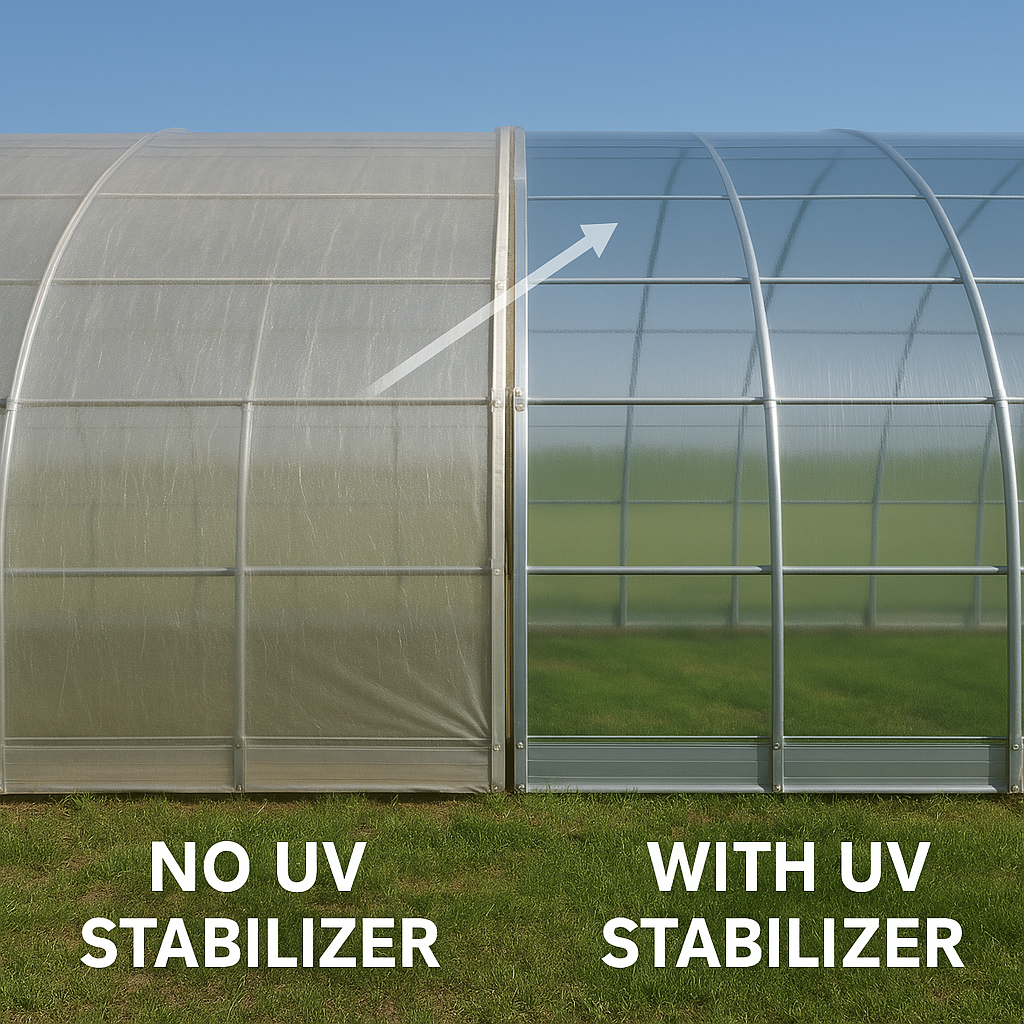
8. Chất tẩy trắng (Whitening Agent):
Trong quá trình sản xuất nhựa, đặc biệt là với nhựa tái sinh, nhựa có chứa tạp chất màu hoặc phối trộn với các phụ gia dễ ngả vàng, màu sắc của thành phẩm thường không đạt độ trắng như mong muốn. Dù vẫn đảm bảo tính năng cơ học, sản phẩm lại bị giảm giá trị cảm quan do ngả vàng, đục mờ hoặc trắng xám. Trong ngành bao bì, nơi yếu tố thị giác quyết định sự thu hút của sản phẩm, điều này là một hạn chế lớn. Để khắc phục vấn đề này, ngành nhựa sử dụng Chất tẩy trắng (Whitening Agent) – phụ gia giúp tăng độ sáng quang học và cải thiện độ trắng tổng thể mà không cần dùng đến hạt màu trắng như TiO₂ với liều cao.
a. Công dụng và tính cần thiết của chất tẩy trắng
- Tăng độ trắng và độ sáng cho sản phẩm nhựa, đặc biệt là nhựa có sắc xám, vàng hoặc hơi đục.
- Khử ám màu vàng, xanh lá hoặc xám nhẹ, thường gặp trong nhựa tái sinh hoặc nhựa chứa nhiều chất phụ gia kỹ thuật.
- Cải thiện tính thẩm mỹ, giúp sản phẩm trông mới, sạch và cao cấp hơn.
- Tăng hiệu ứng phản sáng, giúp sản phẩm có độ bóng và độ trong cao hơn khi nhìn dưới ánh sáng trắng.
- Tăng cường hiệu quả khi dùng chung với hạt màu trắng (Titanium Dioxide), giúp giảm lượng TiO₂ cần sử dụng.
Chất tẩy trắng đặc biệt hữu ích trong bao bì trắng, sản phẩm tiêu dùng, nhựa tái chế, chi tiết trang trí, thiết bị văn phòng và vật liệu trang trí nội thất.
b. Nguyên lý hoạt động
Khác với TiO₂ (chất tạo màu trắng), chất tẩy trắng hoạt động theo cơ chế quang học:
- Hấp thụ ánh sáng tử ngoại (UV) và phát xạ lại dưới dạng ánh sáng xanh tím (fluorescence).
- Điều này tạo cảm giác “trắng hơn” và “sáng hơn” đối với mắt người – tương tự như cách các chất làm trắng trong bột giặt hoạt động.
- Nhờ đó, chúng trung hòa sắc tố vàng, xám nhẹ hoặc xanh lá, giúp sản phẩm có tông màu trắng sáng trung tính.
c. Thành phần và cấu tạo hóa học
Các chất tẩy trắng phổ biến thuộc nhóm Fluorescent Whitening Agent (FWA), hay còn gọi là Optical Brighteners, bao gồm:
- Stilbene derivatives (CBS, OB, OB-1, KSN…):
- Nhóm phổ biến nhất, hiệu quả mạnh, tương thích với nhiều loại nhựa như PE, PP, PS, ABS, PET, PVC.
- OB-1: dùng cho nhựa nhiệt dẻo (PP, PE, PS), có độ bền nhiệt cao (~375°C).
- CBS-X: hòa tan tốt trong nước, phù hợp với masterbatch cho bao bì mềm.
- Benzoxazole derivatives:
- Độ bền ánh sáng cao, dùng trong nhựa cần trưng bày lâu.
- Coumarin, pyrazoline compounds:
- Tạo hiệu ứng làm sáng nhẹ, phù hợp khi cần tẩy trắng tinh tế.
Liều lượng thường dùng rất thấp (50–500 ppm) nhưng hiệu quả thị giác rất rõ rệt.
d. Một số nhãn hiệu và nhà cung cấp nổi bật
- Eastman (Hoa Kỳ):
- Dòng Eastobrite® OB-1, OB-3 – optical brightener chất lượng cao cho nhựa kỹ thuật và bao bì.
- Clariant (Thụy Sĩ):
- Dòng Leucopur® – tẩy trắng chuyên dùng cho màng mỏng, PP, PET, đảm bảo tương thích cao.
- BASF (Đức):
- Dòng Tinopal® – phổ rộng, dùng cho nhựa và masterbatch màu trắng sáng.
- Nantong Senshan (Trung Quốc):
- Nhà cung cấp phổ biến các loại OB, OB-1 cho ngành nhựa tái chế tại châu Á.
- Plastiblends (Ấn Độ):
- Sản xuất masterbatch tẩy trắng tích hợp optical brightener với chất phân tán.
9. Chất tạo ánh tím (Optical Brightener):
Trong ngành bao bì và sản phẩm nhựa tiêu dùng, đặc biệt là các dòng sản phẩm có màu trắng, trong hoặc bán trong suốt, độ sáng và sắc ánh tím nhẹ là dấu hiệu đặc trưng của chất lượng cao, tinh khiết và đẳng cấp thẩm mỹ. Những sản phẩm như hộp mỹ phẩm, túi gói hoa, tấm trang trí, bao bì thực phẩm cao cấp thường mang vẻ “sáng ánh tím” để tạo cảm giác sạch sẽ, mới mẻ và cao cấp. Hiệu ứng này được tạo ra không phải từ màu nhuộm mà nhờ một loại phụ gia đặc biệt: Chất tạo ánh tím (Optical Brightener) – còn được gọi là Chất huỳnh quang làm trắng (Fluorescent Whitening Agent, FWA).
a. Công dụng và tính cần thiết của chất tạo ánh tím
- Tăng độ trắng quang học: làm cho sản phẩm có vẻ sáng hơn, trắng hơn khi nhìn bằng mắt thường.
- Tạo ánh tím hoặc ánh xanh lam nhẹ: trung hòa các tông màu vàng, xám hoặc đục trong nhựa nền.
- Cải thiện cảm giác sạch sẽ, tinh khiết và cao cấp – đặc biệt hiệu quả với bao bì mỹ phẩm, dược phẩm, đồ dùng vệ sinh, sản phẩm trẻ em.
- Hỗ trợ tẩy ngả màu trong nhựa tái chế, cải thiện màu nền mà không cần tăng lượng TiO₂.
- Hiệu ứng mạnh mẽ ngay cả với liều lượng cực thấp (0.01–0.05%), giúp tối ưu chi phí sản xuất.
Chất tạo ánh tím không chỉ là phụ gia thẩm mỹ mà còn là công cụ nâng giá trị cảm quan và cải thiện hình ảnh thương hiệu sản phẩm.
b. Nguyên lý hoạt động
Chất tạo ánh tím hoạt động theo hiện tượng huỳnh quang:
- Hấp thụ tia tử ngoại (UV) trong ánh sáng tự nhiên hoặc nhân tạo.
- Phát xạ lại ánh sáng nhìn thấy được, thường là ánh tím – xanh lam, khiến bề mặt sản phẩm trông sáng hơn, trắng hơn.
- Cơ chế này không làm thay đổi màu sắc nền, mà nâng cấp hiệu ứng thị giác tổng thể.
Hiệu ứng đặc biệt rõ ràng khi sản phẩm được trưng bày dưới ánh đèn huỳnh quang, ánh nắng, hoặc khi đặt cạnh sản phẩm không có optical brightener.
c. Thành phần và cấu tạo hóa học
Các chất tạo ánh tím thường là hợp chất hữu cơ có cấu trúc liên hợp, phổ biến nhất là các dẫn xuất của:
- Stilbene (OB, OB-1, CBS-X):
- Hoạt động mạnh, phổ rộng, giá thành hợp lý.
- OB-1: chịu nhiệt cao, phù hợp với PP, PE, PS, PET.
- CBS-X: tan tốt trong nước, dùng trong masterbatch hoặc sản phẩm cần bề mặt sáng.
- Benzoxazole, Coumarin, Pyrazoline:
- Tạo hiệu ứng ánh tím mượt mà hơn, dùng trong nhựa kỹ thuật hoặc nhựa trong suốt cao cấp.
Tùy loại nhựa nền, nhiệt độ gia công và yêu cầu màu sắc, người ta chọn loại optical brightener tương thích.
d. Một số nhãn hiệu và nhà cung cấp nổi bật
- Clariant (Thụy Sĩ):
- Dòng Leucopur® EGM, Leucopur® 111 – hiệu ứng ánh tím nhẹ, dùng cho bao bì thực phẩm, mỹ phẩm.
- Eastman (Hoa Kỳ):
- Dòng Eastobrite® OB-1, OB-3 – cho nhựa nhiệt dẻo, masterbatch và nhựa tái chế.
- BASF (Đức):
- Dòng Tinopal® OB, CBS-X – chất tạo sáng ánh tím dùng trong nhựa và chất tẩy.
- Senshan Chemical (Trung Quốc):
- OB, OB-1 giá cạnh tranh, dùng cho PP, PE, PS phổ thông tại châu Á.
- ADEKA (Nhật Bản):
- Optical brightener chất lượng cao, ổn định nhiệt và ánh sáng vượt trội.
10. Phụ gia diệt khuẩn (Antibacterial Agent):
Trong bối cảnh người tiêu dùng ngày càng quan tâm đến sức khỏe và vệ sinh, đặc biệt sau đại dịch COVID-19, việc tích hợp tính năng kháng khuẩn, khử khuẩn vào các sản phẩm tiêu dùng đã trở thành một xu hướng tất yếu. Với các vật dụng làm từ nhựa như tay nắm cửa, thiết bị y tế, hộp đựng thực phẩm, bao bì mỹ phẩm hay đồ chơi trẻ em, khả năng chống lại sự phát triển của vi khuẩn trên bề mặt chính là yếu tố nâng cao giá trị sử dụng. Để làm được điều đó, ngành nhựa sử dụng Phụ gia diệt khuẩn (Antibacterial Agent) – một nhóm phụ gia chức năng có khả năng tiêu diệt hoặc ức chế sự phát triển của vi khuẩn, nấm mốc ngay trên bề mặt sản phẩm nhựa.
a. Công dụng và tính cần thiết của phụ gia diệt khuẩn
- Ngăn chặn sự phát triển của vi khuẩn, nấm mốc và vi sinh vật trên bề mặt sản phẩm.
- Giảm nguy cơ lây nhiễm chéo, đặc biệt trong môi trường công cộng, y tế, trường học, nhà hàng, khách sạn…
- Duy trì độ sạch sẽ, không mùi, không nhớt, giúp sản phẩm luôn đạt cảm giác vệ sinh dù được sử dụng nhiều lần.
- Kéo dài tuổi thọ sản phẩm, ngăn biến đổi màu sắc, mùi hôi do nấm mốc hoặc vi khuẩn gây ra.
- Tăng giá trị cảm quan và niềm tin của người dùng, đặc biệt với bao bì thực phẩm, mỹ phẩm và sản phẩm cho trẻ nhỏ.
Phụ gia diệt khuẩn là thành phần thiết yếu trong xu hướng bao bì an toàn, sản phẩm kháng khuẩn và thiết bị y tế sử dụng lâu dài.
b. Nguyên lý hoạt động
Tùy vào loại phụ gia, khả năng diệt khuẩn có thể được thực hiện thông qua:
- Cơ chế ion kim loại (ví dụ: ion bạc Ag⁺):
- Gây tổn thương màng tế bào, phá vỡ chuỗi DNA của vi khuẩn.
- Tác dụng lâu dài, hiệu quả với cả vi khuẩn gram âm và gram dương.
- Cơ chế phá màng tế bào (organic biocide):
- Tác động trực tiếp lên vách tế bào, làm rò rỉ ion và tiêu diệt vi khuẩn ngay lập tức.
- Hiệu quả nhanh, phổ rộng.
- Tạo môi trường kháng khuẩn (pH control, oxygen deprivation):
- Điều chỉnh môi trường bề mặt khiến vi khuẩn khó tồn tại.
Phụ gia thường phân tán đều trong nhựa và dần “di cư” ra bề mặt để duy trì hiệu quả diệt khuẩn lâu dài (up to 5–10 năm tùy loại).
c. Thành phần và cấu tạo hóa học
Một số chất diệt khuẩn phổ biến:
- Nano bạc (Ag⁺) – phổ rộng, an toàn, hiệu quả lâu dài.
- Zinc pyrithione – diệt khuẩn và chống nấm, thường dùng trong PVC, PU, PET.
- Triclosan – hiệu quả cao, nhưng bị hạn chế trong nhiều ngành thực phẩm.
- Quaternary ammonium compounds (QACs) – diệt nhanh, dùng chủ yếu ở dạng coating.
- Chlorinated phenols, isothiazolinone – dùng trong hệ thống kín hoặc sản phẩm không tiếp xúc da.
Dạng sử dụng phổ biến nhất là masterbatch kháng khuẩn, dễ phối trộn và ổn định trong quá trình gia công.
d. Một số nhãn hiệu và nhà cung cấp nổi bật
- Sanitized AG (Thụy Sĩ):
- Chuyên các dòng phụ gia diệt khuẩn dùng trong nhựa, sơn và dệt may – có chứng nhận an toàn thực phẩm và y tế.
- Sciessent (Hoa Kỳ):
- Dòng Agion® – nano bạc thế hệ mới, có thể dùng trong thiết bị y tế và sản phẩm trẻ em.
- Microban® (Hoa Kỳ):
- Giải pháp toàn diện tích hợp kháng khuẩn cho nhiều vật liệu, từ nhựa đến cao su và gỗ ép.
- Plastiblends (Ấn Độ):
- Cung cấp masterbatch diệt khuẩn phù hợp với PE, PP, PET, ABS.
- Nobel (Trung Quốc):
- Dòng Ag masterbatch phổ thông, dùng cho bao bì thực phẩm, đồ chơi, túi kháng khuẩn.
11. Chất trượt (Slip Agent):
Trong quá trình sản xuất và sử dụng sản phẩm nhựa – đặc biệt là màng nhựa, bao bì mềm, túi nilon, tấm film đa lớp, hiện tượng bám dính giữa các lớp hoặc lực ma sát quá lớn thường gây trở ngại cho gia công và sử dụng: màng khó cuộn, bao khó mở, bề mặt dễ xước hoặc kẹt khi chạy máy. Để khắc phục những vấn đề này, ngành nhựa sử dụng một loại phụ gia chuyên biệt: Chất trượt (Slip Agent) – phụ gia giúp giảm hệ số ma sát (COF) của bề mặt nhựa, giúp sản phẩm dễ trượt, ít bám dính và chạy máy mượt mà hơn.
a. Công dụng và tính cần thiết của chất trượt
- Giảm ma sát giữa các bề mặt nhựa, giúp sản phẩm dễ tách lớp, dễ cuộn, dễ đóng gói.
- Cải thiện khả năng vận hành máy móc, giảm hiện tượng kẹt, xước, rách trong quá trình cán màng, cắt cuộn, thổi túi.
- Tăng cảm giác mượt tay, mềm mại khi cầm nắm, nâng cao trải nghiệm người dùng.
- Hạn chế bám bụi và tĩnh điện, đặc biệt quan trọng trong bao bì thực phẩm, y tế và điện tử.
- Tạo hiệu ứng trượt một chiều trong các loại túi zipper, bao bì kỹ thuật.
Chất trượt là phụ gia thiết yếu trong sản xuất màng PE, PP, BOPP, bao bì co giãn, túi nilon siêu mỏng và các loại film đa lớp.
b. Nguyên lý hoạt động
Chất trượt thường là các phân tử có khả năng di cư (migrate) từ bên trong ra bề mặt nhựa sau khi tạo hình:
- Tạo thành một lớp màng siêu mỏng, có khả năng tự bôi trơn, giúp bề mặt giảm lực ma sát tĩnh và động.
- Một số loại còn hoạt động như chất phân cách vi mô, ngăn hai lớp màng không dính sát vào nhau.
Tùy vào cấu trúc và tốc độ di cư, người ta chọn chất trượt để tạo hiệu ứng trượt nhanh – chậm, phù hợp với từng ứng dụng.
c. Thành phần và cấu tạo hóa học
Các nhóm chất trượt phổ biến bao gồm:
- Amide tự nhiên và tổng hợp:
- Erucamide – hiệu ứng trượt tốt, di cư ổn định, phổ biến nhất trong PE, BOPP.
- Oleamide – tốc độ di cư nhanh, hiệu ứng ban đầu mạnh, dùng trong sản phẩm cần hiệu ứng sớm.
- Stearamide – hiệu ứng nhẹ, dùng khi cần độ trượt vừa phải và lâu dài.
- Siloxane (organosilicone):
- Tạo bề mặt trơn cao cấp, ít ảnh hưởng đến in ấn, dùng trong film kỹ thuật hoặc sản phẩm có phủ sau.
- Khả năng chịu nhiệt và ổn định bề mặt rất tốt.
- Ester sáp và polymer trượt:
- Tạo hiệu ứng trượt nhẹ nhàng, mềm mại, phù hợp bao bì cao cấp hoặc sản phẩm cần cảm giác chạm.
- Masterbatch chứa slip agent:
- Phối trộn sẵn với nhựa nền, dễ sử dụng, hiệu quả ổn định.
d. Một số nhãn hiệu và nhà cung cấp nổi bật
- Croda Polymer Additives (Anh):
- Dòng Incroslip® – erucamide, oleamide chất lượng cao, hiệu ứng ổn định.
- Fine Organics (Ấn Độ):
- Dòng Finawax® E, O, S – chất trượt dạng bột hoặc masterbatch, được dùng phổ biến tại châu Á.
- Clariant (Thụy Sĩ):
- Dòng AddWorks® LXR – phụ gia trượt kết hợp chất chống dính và chất phân tán.
- BYK (Đức):
- Dòng BYK-Silicone Additives – chất trượt gốc siloxane cho nhựa kỹ thuật và màng in.
- Ampacet (Hoa Kỳ):
- Masterbatch trượt tùy chỉnh, có thể kết hợp chống dính, kháng UV hoặc chống tĩnh điện
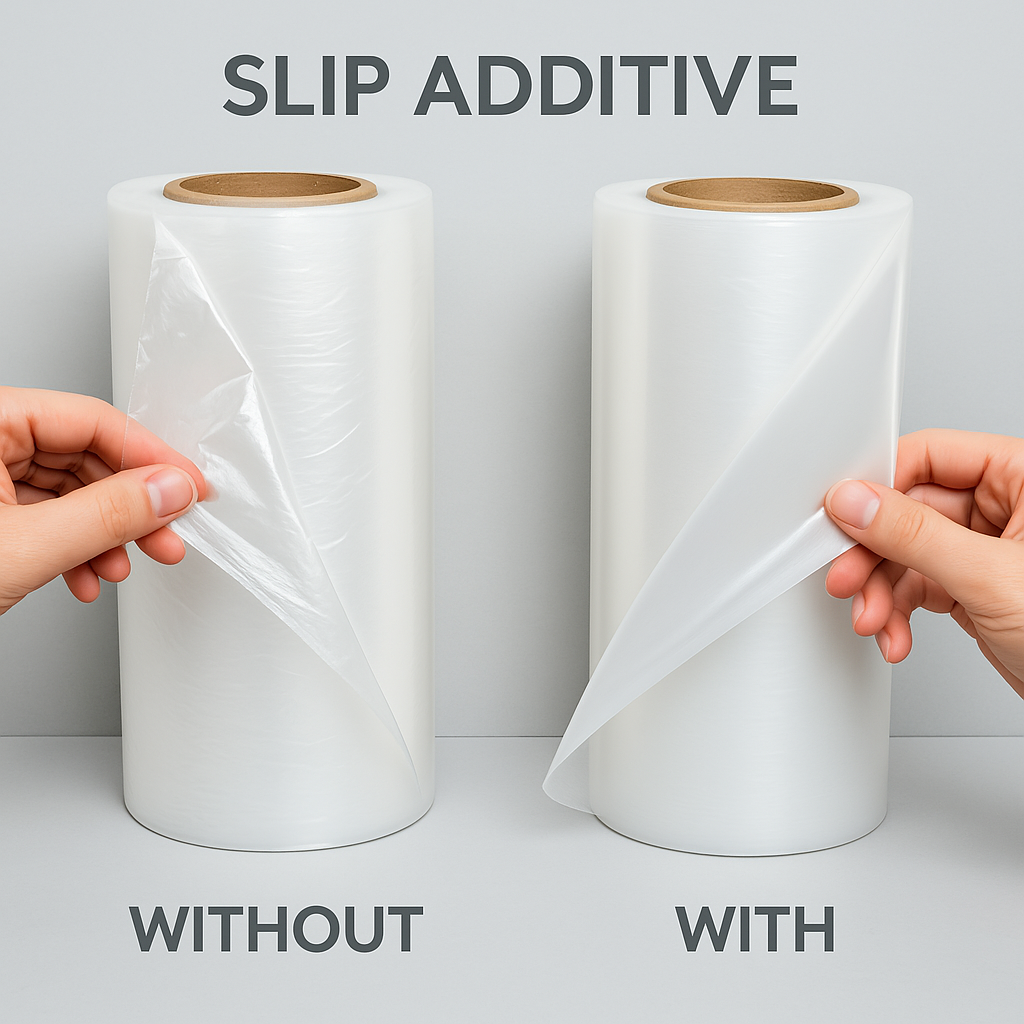
12. Chất chống dính (Anti-blocking Agent):
Trong sản xuất màng nhựa mỏng như PE, PP, BOPP, PET, hiện tượng hai lớp màng dính chặt vào nhau sau khi đùn hoặc cuộn – còn gọi là blocking – là vấn đề phổ biến gây ảnh hưởng nghiêm trọng đến quá trình gia công, đóng gói và sử dụng. Blocking xảy ra do bề mặt nhựa nóng chảy khi nguội tạo ra liên kết bề mặt mạnh, đặc biệt khi cuộn với lực ép cao hoặc lưu trữ trong môi trường nóng ẩm. Để khắc phục tình trạng này, ngành nhựa sử dụng Chất chống dính (Anti-blocking Agent) – phụ gia tạo khoảng cách vi mô giữa các lớp màng, giúp sản phẩm dễ tách lớp, dễ mở túi và vận hành trơn tru trên máy móc.
a. Công dụng và tính cần thiết của chất chống dính
- Ngăn hiện tượng hai lớp màng dính chặt vào nhau, đặc biệt sau quá trình cuộn, ép hoặc lưu trữ.
- Tạo khả năng tách lớp dễ dàng, giúp quá trình đóng gói, mở túi hoặc gia công tự động trở nên mượt mà.
- Cải thiện hiệu suất vận hành máy cắt, máy in, máy đóng gói, tránh kẹt màng hoặc kéo rách sản phẩm.
- Giảm thiểu lượng hư hỏng do ma sát bề mặt hoặc bám dính cơ học, giúp màng mịn và sạch hơn.
- Tăng giá trị cảm quan và khả năng sử dụng của các loại túi mềm, túi zipper, màng phủ, màng co…
Chất chống dính đặc biệt quan trọng trong bao bì thực phẩm, màng cuộn tự động, film công nghiệp, màng nhựa dùng trong đóng gói tốc độ cao.
b. Nguyên lý hoạt động
Chất chống dính là các hạt rắn siêu mịn, phân tán đều trong lớp màng nhựa, tạo ra:
- Hiệu ứng nhám vi mô (microscopic roughness) trên bề mặt, làm giảm diện tích tiếp xúc giữa hai lớp màng.
- Khoảng cách siêu nhỏ giữa các lớp, khiến bề mặt không tạo liên kết chặt khi ép sát vào nhau.
- Tùy vào kích thước và mật độ hạt, hiệu ứng chống dính có thể được điều chỉnh theo yêu cầu.
c. Thành phần và cấu tạo hóa học
Các chất chống dính thường là vật liệu vô cơ trơ, có độ cứng cao, ổn định nhiệt và không ảnh hưởng đến tính chất cơ học của nhựa:
- Silica (SiO₂) tự nhiên hoặc kết tủa:
- Dạng phổ biến nhất, hiệu quả cao, bề mặt trơ và ổn định.
- Có thể điều chỉnh kích thước hạt từ 2–8 micron tùy ứng dụng.
- Talc, Kaolin, Diatomite (đất tảo):
- Giá rẻ, hiệu quả vừa phải, dùng trong màng dày hoặc nhựa tái sinh.
- Calcium carbonate (CaCO₃) siêu mịn:
- Kết hợp tác dụng chống dính và tăng cứng, nhưng hiệu ứng không mạnh bằng silica.
- Polystyrene beads, PMMA particles:
- Dùng trong màng kỹ thuật cao cấp, tấm film quang học hoặc sản phẩm in chất lượng cao.
- Blend với slip agent hoặc chất phân tán:
- Để tăng hiệu quả chống dính và duy trì độ bóng bề mặt.
d. Một số nhãn hiệu và nhà cung cấp nổi bật
- Evonik (Đức):
- Dòng Sipernat®, AEROSIL® – silica chống dính siêu mịn, hiệu quả ổn định và dễ phối trộn.
- W.R. Grace (Hoa Kỳ):
- Dòng SYLOBLOC® – chuyên dùng cho màng PE, BOPP, PET, có thể phối hợp chất trượt.
- Clariant (Thụy Sĩ):
- Dòng AddWorks® AB – chất chống dính tích hợp trong masterbatch.
- Ampacet (Hoa Kỳ):
- Cung cấp masterbatch chống dính + trượt, dùng cho bao bì thực phẩm tốc độ cao.
- Fine Organics (Ấn Độ):
- Dòng Finawax AB Series – phụ gia tự nhiên có hiệu ứng nhẹ, dùng cho sản phẩm thân thiện môi trường.
13. Phụ gia tạo mùi hương (Fragrance Additive):
Trong một thế giới nơi người tiêu dùng ngày càng chú trọng đến trải nghiệm cảm quan đa giác quan, mùi hương trở thành một yếu tố tinh tế nhưng mạnh mẽ để truyền tải thông điệp thương hiệu, tạo cảm xúc và kết nối với người dùng. Trong ngành bao bì nhựa, một chiếc túi thơm nhẹ mùi vani, oải hương hay trái cây không còn là điều xa lạ – đó là thành quả của việc tích hợp Phụ gia tạo mùi hương (Fragrance Additive) vào hạt nhựa. Loại phụ gia này vừa đảm bảo tính ổn định trong quá trình gia công, vừa giúp giữ được mùi thơm dễ chịu trong thời gian dài, tạo nên giá trị cảm quan khác biệt cho sản phẩm.
a. Công dụng và tính cần thiết của phụ gia tạo mùi hương
- Tạo mùi thơm đặc trưng cho sản phẩm nhựa, giúp phân biệt, định vị và nâng cao trải nghiệm người dùng.
- Khử mùi nguyên liệu nhựa tái sinh hoặc chất phụ gia kỹ thuật, đặc biệt là mùi khét, mùi nhựa cháy hoặc mùi hoá học.
- Tăng cảm giác sạch sẽ, tươi mới, cao cấp cho bao bì, đặc biệt trong mỹ phẩm, quà tặng, thời trang, thực phẩm khô.
- Hỗ trợ chiến lược thương hiệu, khi mùi hương được đồng bộ hóa với màu sắc, thiết kế và đối tượng người dùng.
- Không ảnh hưởng đến tính cơ học hoặc an toàn vệ sinh thực phẩm, nếu chọn loại phụ gia đạt chuẩn.
Phụ gia tạo hương là điểm nhấn đặc biệt trong bao bì mỹ phẩm, túi quà, bao bì cao cấp, đồ chơi trẻ em, sản phẩm văn phòng và nhựa tiêu dùng thân thiện người dùng.
b. Nguyên lý hoạt động
Phụ gia tạo mùi hương được chế tạo dưới dạng vi nang hoặc chất mang hương thơm tích hợp vào hạt nhựa:
- Trong quá trình ép đùn, mùi hương không bị bốc hơi hoàn toàn nhờ kỹ thuật microencapsulation (bao vi nang) hoặc polymer carrier có khả năng giữ hương.
- Sau khi tạo hình, hương thơm thoát ra từ từ qua các lỗ vi mô trên bề mặt, tạo ra hiệu ứng thơm nhẹ, kéo dài trong thời gian sử dụng.
- Một số loại còn được thiết kế để tỏa hương khi ma sát hoặc mở bao bì, tăng hiệu ứng trải nghiệm.
c. Thành phần và cấu tạo hóa học
Phụ gia tạo mùi hương thường bao gồm:
- Tinh dầu tự nhiên hoặc hương tổng hợp:
- Vani, hoa nhài, oải hương, bạc hà, cam quýt, sôcôla, dâu, dưa gang, dứa…
- Được chọn lọc kỹ để đảm bảo không gây dị ứng, không độc hại.
- Chất mang (carrier):
- PE wax, EVA, PP resin – giúp giữ hương và ổn định khi gia công nhiệt.
- Một số loại dùng polymer xốp hoặc vi cầu PMMA để chứa hương.
- Vi nang hoặc chất ổn định mùi:
- Giúp kiểm soát tốc độ thoát hương, kéo dài thời gian lưu hương trên bề mặt.
d. Một số nhãn hiệu và nhà cung cấp nổi bật
- Kao Chemicals (Nhật Bản):
- Dòng Fragrance Masterbatch, hương nhẹ nhàng, bền mùi, dùng cho PE, PP.
- Polyvel (Hoa Kỳ):
- Dòng Fragrance Carriers, chuyên cho sản phẩm cao cấp, có thể in mùi lên sản phẩm.
- Plastiblends (Ấn Độ):
- Masterbatch hương sẵn có với nhiều lựa chọn: dâu, cam, táo, hoa… giá hợp lý.
- Shandong Yihua (Trung Quốc):
- Cung cấp masterbatch tạo mùi phổ thông, dùng cho bao bì tiêu dùng và đồ chơi.
- Microban® (Hoa Kỳ):
- Dòng Scentry® – kết hợp tính năng kháng mùi và tạo mùi dễ chịu trong một hệ phụ gia.
14. Phụ gia phân hủy sinh học (Biodegradable Additive):
Trong bối cảnh ô nhiễm nhựa trở thành một vấn đề toàn cầu và nhu cầu phát triển bền vững ngày càng được coi trọng, ngành nhựa đang đứng trước yêu cầu phải đổi mới – không chỉ trong thiết kế sản phẩm mà còn trong bản chất vật liệu. Một trong những hướng đi chiến lược được ưu tiên là phát triển nhựa có khả năng phân hủy sinh học, giúp giảm thiểu rác thải tồn lưu lâu dài trong môi trường tự nhiên. Để hiện thực hóa điều này mà vẫn giữ được quy trình sản xuất truyền thống, các nhà sản xuất sử dụng Phụ gia phân hủy sinh học (Biodegradable Additive) – phụ gia có khả năng cải biến cấu trúc phân tử nhựa, giúp vi sinh vật nhận diện và phân hủy vật liệu nhanh chóng hơn trong điều kiện tự nhiên hoặc công nghiệp.
a. Công dụng và tính cần thiết của phụ gia phân hủy sinh học
- Biến đổi nhựa thông thường (như PE, PP, PS) thành loại vật liệu có khả năng phân hủy bởi vi sinh vật trong đất, nước, hoặc môi trường ủ công nghiệp.
- Giúp sản phẩm nhựa sau sử dụng không tồn đọng hàng trăm năm, mà có thể biến mất trong vòng vài tháng đến vài năm tùy điều kiện.
- Đáp ứng yêu cầu của các tiêu chuẩn môi trường và chính sách hạn chế nhựa dùng một lần (như EN13432, ASTM D6400, ISO 17088…).
- Không ảnh hưởng đến tính chất cơ lý trong thời gian sử dụng, tức là sản phẩm vẫn dùng như nhựa thường, nhưng sau đó sẽ tự hủy.
- Tạo lợi thế thương hiệu về trách nhiệm môi trường, rất quan trọng trong ngành bao bì thực phẩm, thời trang, logistic, dịch vụ ăn uống và nông nghiệp.
Phụ gia phân hủy sinh học là thành phần cốt lõi trong xu hướng sản xuất nhựa sinh thái, bao bì thân thiện môi trường, túi phân hủy, màng phủ nông nghiệp, nhựa tái tạo hoặc nhựa pha bột hữu cơ.
b. Nguyên lý hoạt động
Phụ gia phân hủy sinh học thường hoạt động theo ba cơ chế chính:
- Tạo điểm gãy (pro-degradant) trong chuỗi polymer, giúp cấu trúc nhựa dễ bị cắt đứt hơn bởi nhiệt, ánh sáng hoặc vi sinh.
- Cung cấp chất xúc tác sinh học hoặc môi trường thuận lợi cho vi khuẩn, nấm mốc tiêu hóa vật liệu nhựa.
- Làm tăng khả năng ẩm ướt và hấp thụ của nhựa, tạo điều kiện vi sinh vật tiếp cận và phá vỡ chuỗi carbon.
Một số phụ gia còn kích hoạt cơ chế phân rã chỉ sau một thời gian sử dụng, giúp sản phẩm bền trong tay người dùng nhưng dễ phân hủy sau khi thải bỏ.
c. Thành phần và cấu tạo hóa học
Các nhóm phụ gia phân hủy sinh học phổ biến:
- Oxo-biodegradable additive:
- Gốc kim loại chuyển tiếp như Mn, Fe, Co… kết hợp với polyolefin.
- Tạo gốc tự do khi tiếp xúc UV hoặc oxy, làm gãy chuỗi polymer.
- Enzyme or microbial trigger additives:
- Cung cấp enzyme hoặc chất dinh dưỡng kích thích vi sinh vật phân hủy vật liệu.
- Starch-based carrier, PLA, PBAT blend:
- Pha trộn với nhựa nền, giúp tăng tính tương hợp sinh học và hấp thụ nước.
- Polyester-based modifiers (PCL, PBS):
- Phân hủy hoàn toàn trong điều kiện hiếu khí hoặc ủ công nghiệp.
- Natural oil derivatives:
- Tăng khả năng oxy hóa và hấp thụ ẩm, dùng trong bao bì mềm.
d. Một số nhãn hiệu và nhà cung cấp nổi bật
- EPI Environmental Products Inc. (Canada):
- Dòng TDPA® (Totally Degradable Plastic Additive) – phụ gia phân hủy nổi tiếng trong túi PE, bao bì dùng một lần.
- Symphony Environmental (Anh):
- Dòng d2w® – oxo-biodegradable được ứng dụng tại hơn 90 quốc gia.
- BioSphere Plastic (Hoa Kỳ):
- Phụ gia sinh học kết hợp enzyme, phân hủy được cả nhựa PE, PP, PS, PET.
- Plastiblends (Ấn Độ):
- Cung cấp masterbatch phân hủy sinh học giá hợp lý, dùng cho bao bì tiêu dùng.
- GreenMantra (Canada):
- Chuyên sản xuất phụ gia thân thiện môi trường từ nhựa tái chế có khả năng phân hủy tự nhiên
15. Phụ gia tự phân hủy (Oxo-biodegradable Additive):
Trong nỗ lực giảm thiểu ô nhiễm nhựa và hướng tới nền kinh tế tuần hoàn, một trong những công nghệ nổi bật được ứng dụng rộng rãi là phụ gia tự phân hủy (Oxo-biodegradable Additive). Đây là loại phụ gia được thiết kế để bổ sung trực tiếp vào nhựa truyền thống như PE, PP, PS, giúp các sản phẩm có khả năng tự phân hủy sau thời gian sử dụng mà không cần thay đổi công nghệ sản xuất. Nhờ tính ứng dụng linh hoạt và chi phí thấp, oxo-biodegradable đã trở thành lựa chọn phổ biến cho túi nilon, bao bì thực phẩm, túi đựng rác, màng phủ nông nghiệp và các sản phẩm nhựa dùng một lần.
a. Công dụng và tính cần thiết của phụ gia tự phân hủy
- Kích hoạt quá trình phân hủy của nhựa thông thường khi tiếp xúc với ánh sáng, nhiệt độ và oxy.
- Rút ngắn thời gian tồn tại của sản phẩm nhựa ngoài môi trường – từ hàng trăm năm xuống còn vài năm hoặc vài tháng tùy điều kiện.
- Giữ nguyên tính chất cơ học và hình thức của sản phẩm trong quá trình sử dụng, không ảnh hưởng đến độ bền, độ dẻo hay khả năng in ấn.
- Dễ tích hợp vào quy trình sản xuất hiện tại chỉ bằng cách trộn vào hạt nhựa với tỉ lệ nhỏ (thường 1–3%).
- Tối ưu chi phí và dễ triển khai đại trà, là giải pháp ngắn hạn hiệu quả để giảm lượng nhựa tích tụ ngoài thiên nhiên.
Oxo-biodegradable là lựa chọn lý tưởng trong các sản phẩm nhựa không tái chế sau sử dụng, có vòng đời ngắn, thường bị thải ra môi trường công cộng hoặc bãi rác.
b. Nguyên lý hoạt động
Phụ gia oxo-biodegradable hoạt động qua hai giai đoạn:
- Giai đoạn phân cắt (Oxo-degradation):
- Dưới tác động của tia UV, oxy và nhiệt độ môi trường, các gốc hoạt tính trong phụ gia (thường là muối kim loại như sắt, mangan, coban) phá vỡ chuỗi polymer dài thành các phân tử nhỏ hơn – làm nhựa mất dần tính bền và trở nên giòn, dễ vụn.
- Giai đoạn phân hủy sinh học (Biodegradation):
- Các phân tử nhỏ sau giai đoạn đầu trở thành nguồn dinh dưỡng cho vi sinh vật trong đất, từ đó được chuyển hóa thành CO₂, H₂O, và sinh khối.
Toàn bộ quá trình có thể mất 6 tháng đến vài năm, tùy điều kiện khí hậu, độ dày sản phẩm và hàm lượng phụ gia.
c. Thành phần và cấu tạo hóa học
Các phụ gia oxo-biodegradable thường chứa:
- Muối kim loại xúc tác oxi hóa:
- Sắt (Fe), Mangan (Mn), Cobalt (Co), Canxi (Ca) – tạo phản ứng oxy hóa nhẹ khi tiếp xúc với ánh sáng và không khí.
- Chất xúc tiến phản ứng nhiệt – UV:
- Giúp rút ngắn thời gian bắt đầu phân hủy sau khi sản phẩm hoàn thành vòng đời sử dụng.
- Chất ổn định trong quá trình gia công:
- Bảo vệ phụ gia khỏi phân hủy sớm khi gia công ở nhiệt độ cao (160–230°C).
- Hệ mang (carrier resin):
- PE, PP hoặc EVA – giúp phân tán đồng đều phụ gia trong hạt nhựa nguyên sinh.
d. Một số nhãn hiệu và nhà cung cấp nổi bật
- Symphony Environmental (Anh):
- Dòng d2w® – thương hiệu oxo-biodegradable nổi tiếng, đã có mặt tại hơn 90 quốc gia.
- EPI Environmental (Canada):
- Dòng TDPA® (Totally Degradable Plastic Additive) – được ứng dụng rộng rãi cho túi siêu thị, bao bì logistic.
- Willow Ridge Plastics (Hoa Kỳ):
- Dòng Reverte® – chuyên dùng trong film PE, màng phủ nông nghiệp và bao bì phân bón.
- Plastiblends (Ấn Độ):
- Cung cấp masterbatch oxo với giá thành hợp lý cho thị trường châu Á.
- BIO-Tec Environmental (Hoa Kỳ):
- Dòng EcoPure® – công nghệ pha trộn có khả năng tự phân hủy trong điều kiện bãi rác.
Thế giới phụ gia trong sản xuất bao bì nhựa là một hệ thống kỹ thuật tinh vi, đóng vai trò không thể thay thế trong việc định hình chất lượng, giá trị và bản sắc của mỗi chiếc túi nilon. Việc lựa chọn và phối trộn đúng loại phụ gia không chỉ giúp tối ưu quy trình sản xuất mà còn tạo nên những sản phẩm có tính năng ưu việt, thẩm mỹ cao và phù hợp với xu hướng tiêu dùng hiện đại.