Hầu hết các loại nhựa nhiệt dẻo như polyethylene mật độ thấp (LDPE), polypropylene (PP), polyethylene mật độ cao (HDPE), nylon/ polyamide (PA), copolyme ethylene-vinyl axetat (EVA), đều có thể được sản xuất bằng quy trình đùn thổi để tạo thành màng.
Và trong suốt quá trình sản xuất túi nhựa ở bất kỳ chất liệu nào, nhiều sai sót và trục trặc luôn có thể xảy ra, cả chủ quan và khách quan, cả do yếu tố con người lẫn lỗi ở hệ thống thiết bị.
Ở bài viết này, chúng tôi xin giới thiệu ngắn gọn các khái niệm và thông số cần được nắm rõ trong quy trình sản xuất đúc thổi màng polyetylen mật độ thấp (LDPE).
1. Tầm quan trọng của việc chọn lựa nguyên liệu hạt nhựa
Nếu không tính đến hạt nhựa tái chế, chỉ riêng hạt nhựa LDPE dạng nguyên sinh, thì cũng đã có rất nhiều chủng loại, với các mã hạt nhựa khác nhau như FT6230, 2426K, C150Y, 2427K,… Mỗi loại trong số chúng lại có những thông số kỹ thuật và tiêu chuẩn an toàn riêng, tùy thuộc vào nhà sản xuất.
Trong các chỉ số đó, chỉ số nóng chảy (MI) là một thông số khá quan trọng. Nếu chỉ số nóng chảy quá lớn thì độ nhớt của nhựa nóng chảy sẽ quá nhỏ, khiến phạm vi xử lý bị thu hẹp, quy trình sản xuất trở nên khó kiểm soát. Sản phẩm thu được sau quá trình đùn thổi sẽ có đặc tính tạo màng kém , gây khó khan cho việc gia công, chế biến thành màng hay túi nhựa.
Chỉ số nóng chảy MI của hạt nhựa quá lớn cũng dẫn đến phân bố trọng lượng phân tử tương đối của polyme bị thu hẹp, làm kém đi độ bền chắc vốn có của vật liệu.
Hạt nhựa LDPE có chỉ số nóng chảy nhỏ, nằm trong khoảng khoảng 2 ~ 6g / 10 phút được cho là lý tưởng cho sản xuất bao bì nhựa.
Cần lưu ý là hạt nhựa LDPE nguyên sinh cũng chia làm 2 cấp độ. Một loại dùng cho sản xuất màng bằng phương pháp đùn thổi, và một loại dùng cho phương pháp đùn đúc. Loại dùng cho màng thổi có chứa chất trơn trượt giúp cho túi nhựa không bị dính chặt, gây khó khăn khi mở miệng túi.
2. Các thông số kỹ thuật của máy đùn thổi màng nhựa
Trên hệ thống máy thổi túi nhựa, sẽ tồn tại nhiều thông số kỹ thuật cần được canh chỉnh. Tốc độ của motor quấn trục, lưu lượng khí nén bơm vào màng, nhiệt độ và tốc độ đẩy của trục vít đùn nhựa ,.. Kích thước, độ dày và các đặc tính của màng sẽ được quyết định bằng sự điều chỉnh kết hợp các thông số này.
a. Tỷ lệ giãn nở hay còn gọi là tỷ lệ thổi
Đây là thông số quyết định kích thước chiều ngang tối đa của màng nhựa, mà một cỗ máy thổi có thể sản xuất được. Tỷ lệ giãn nở hay tỷ lệ thổi lên chính là tỷ lệ giữa đường kính của bong bóng màng sau khi đã được bơm căng bằng khí nén và đường kính của màng khi mới vừa được đùn ra khỏi đầu khuôn thổi, tính bằng bội số.
Đối với vật liệu LDPE, thông số lý tưởng cho tỷ lệ này là từ 2,5 cho đến 3. Điều đó có nghĩa là nếu đường kính đầu khuôn thổi có kích thước 10cm, thì sẽ phù hợp để thổi lên bong bóng nhựa có đường kính từ 25 đến 30 cm. Để có được chiều ngang của cuộn màng thành phẩm, ta nhân đường kính này với số Pi. Ở ví dụ trên, ta có được kích cỡ tối đa của màng nhựa LDPE có thể sản xuất được là từ 39 đến 41 cm.
Có thể thấy, tỷ lệ thổi là bội số giãn nở theo chiều ngang của màng. Để điều chỉnh sự giãn nở này, người ta bơm thêm khí nén vào nếu muốn tăng lên, hoặc dùng vật nhọn chọc thủng, xì bớt không khí trong bong bóng màng ra ngoài, nếu muốn giảm xuống. Trong quá trình máy hoạt động, lỗ thủng giúp giảm lượng khí nén trong bong bóng nhựa sẽ nhanh chóng được cuốn lên và quấn vào cuộn màng theo chuyển động của con lăn, nên sẽ hoàn toàn không có tình trạng khí nén bị thoát hết toàn bộ ra ngoài theo lỗ thủng này.
Việc màng nhựa được kéo căng theo hướng ngang sẽ có tác động định hướng ở một mức độ nhất định đối với các phân tử nhựa. Và do đó, tỷ lệ thổi sẽ tỷ lệ thuận với độ dày của lớp màng. Màng càng dày thì tỷ lệ thổi phải càng lớn. Và độ dày mỏng của màng thì lại được quyết định bởi một thông số khác, đó là tỷ lệ lực kéo.
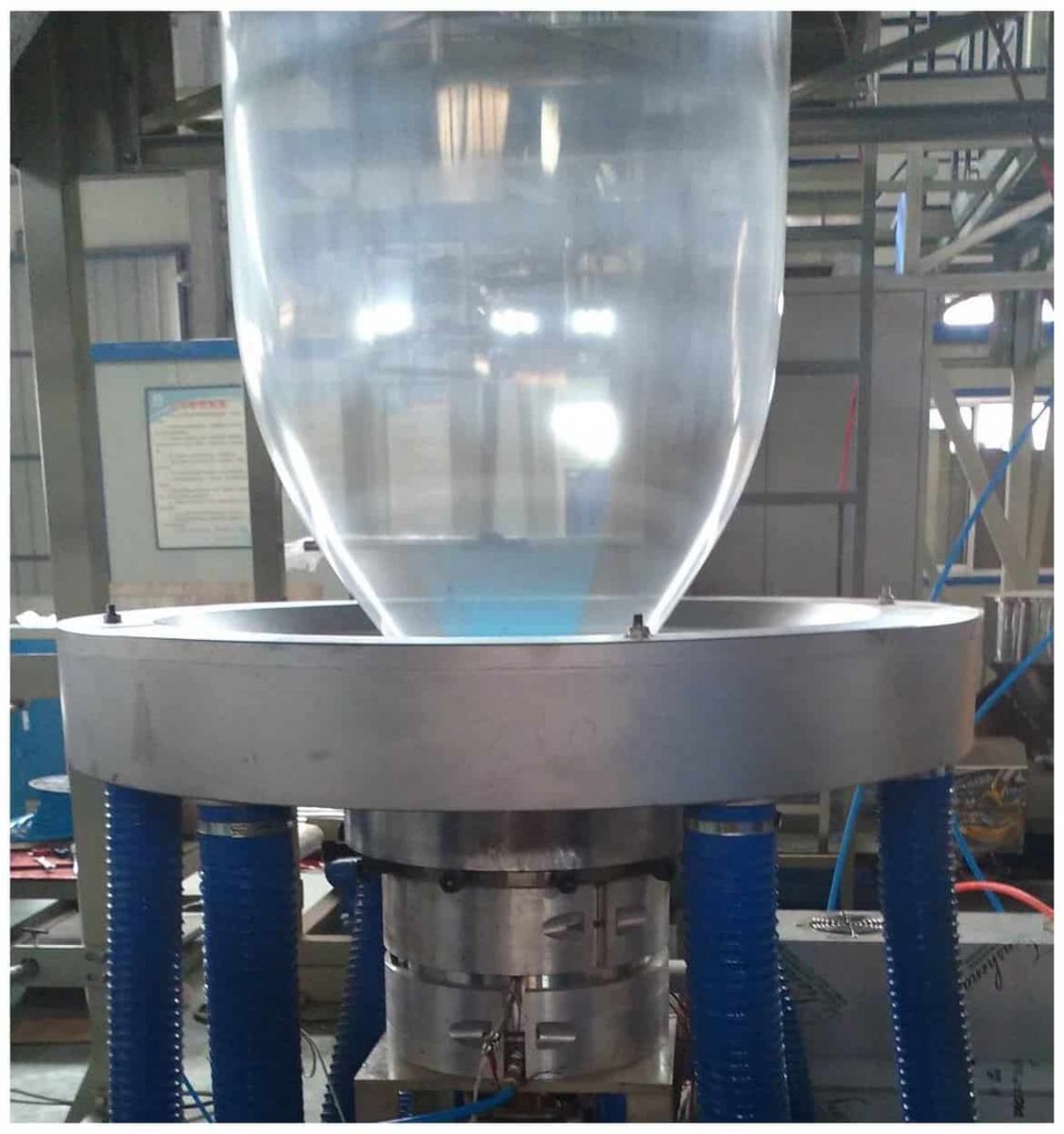
b. Tỷ lệ kéo lên hay còn gọi là tỷ lệ lực kéo
Tỷ lệ hay tỷ số lực kéo, là bội số giữa tốc độ kéo lên bởi con lăn của màng và tốc độ đùn của trục đùn, trên cùng một đơn vị thời gian. Ví dụ như trong một giây, trục đùn đẩy ra được 5 cm chiều dài ống màng nhựa, mà chiều dài của ống màng này được kéo lên qua các trục lăn kéo và con lăn dẫn hướng là 25 cm, thì chúng ta sẽ có tỷ số lực kéo 25/ 5= 5. Tỷ số lực kéo này luôn lớn hơn 1. Dưới trị số này, bong bóng nhựa sẽ bị biến dạng và quy trình thổi thất bại.
Chiều dài của cuộn màng được kéo lên qua con lăn luôn lớn hơn chiều dài của màng được đẩy ra khỏi trục đùn. Có nghĩa là, màng nhựa đùn ra đã được kéo dãn và định hướng phân tử theo chiều dọc hay nói dễ hiểu hơn là chúng đã bị kéo dài ra. Tỷ số lực kéo càng tăng, thì màng càng được kéo dãn, độ dày sẽ càng mỏng hơn và ngược lại.
Tuy nhiên chỉ số này cũng có một khoảng giới hạn, bởi màng quá mỏng thì sẽ dễ bị vỡ bởi áp suất khí nén. Màng quá dày thì lại không đủ thời gian để nguội đi, đồng thời mất đi tính định hình, dễ bị biến dạng. Với những yêu cầu quá cao về độ dày, người ta phải sử dụng phương pháp đùn đúc. Ở phương pháp này, màng nhựa sẽ được đùn từ trên xuống một cách chậm rãi, và tỷ số lực kéo có thể điều chỉnh xuống mức thấp nhất.
Tỷ lệ lực kéo khi thổi màng polyethylene mật độ thấp (LDPE) nằm trong khoảng từ 4 đến 6. Đây là trị số được cho là sẽ đem lại khả năng kiểm soát và hiệu suất tốt nhất cho dây chuyền sản xuất bằng phương pháp đùn thổi.
c. Nhiệt độ máy đùn
Đối với màng polyethylene mật độ thấp (LDPE), nhiệt độ của trục đùn thường được kiểm soát từ 160 ° C đến 170 ° C. Nhiệt độ này cần phải đồng đều ở khắp mọi điểm dọc theo chiều dài của trục. Nhiệt độ đùn quá cao, cấu trúc nhựa dễ bị phân hủy, và màng sẽ bị giòn. Ngược lại nếu nhiệt độ quá thấp, nhựa sẽ không thể tan chảy hết, dẫn đến bề mặt sần sùi và độ dày của màng bị sai lệch. Trong cả hai trường hợp, hiệu suất của màng đều giảm đi đáng kể, và quy trình sản xuất sẽ trở nên vô cùng khó kiểm soát.
d. Điểm mờ
Điểm mờ hay còn được gọi là đường sương, đường mờ, là một vệt ngang có thể nhìn thấy rõ ở phần dưới đáy của bong bóng nhựa đang được thổi lên. Đường ngang này không phải là một điểm cố định trên màng, mà thực chất là vị trí mà nhựa sẽ chuyển đổi trạng thái màu sắc của chúng từ trong suốt sang mờ đục.
Nguyên nhân của sự chuyển đổi màu sắc này là do nhựa được thay đổi đặc tính, từ trạng thái hơi lỏng và nhớt khi mới được nung chảy, sang trạng thái khô và đàn hồi cao khi được kéo dãn và làm mát đột ngột bởi vòng khí làm mát được gắn ngay trên đầu khuôn thổi.
Với những dây chuyền sản xuất màng nhựa không có hệ thống cảm biến đo kích thước và độ dày hiện đại, chính điểm mờ này sẽ là yếu tố quan trọng, giúp những người công nhân vận hành máy biết được sản phẩm tạo ra đang có được hiệu năng tốt nhất hay không.
Lý tưởng nhất là khi điểm mờ này nằm ngay vị trí mà bong bóng màng bắt đầu phình to kích thước. Điểm mờ nằm cao hơn vị trí này, có nghĩa là các phân tử nhựa bị kéo căng khi nhựa vẫn còn đang trong trạng thái lỏng, khiến việc định hướng phân tử có nguy cơ xảy ra không đồng đều. Sản phẩm thu được sẽ có độ dày mỏng không đồng nhất trên mọi điểm. Đây là sai sót rất thường xảy ra và cũng khó phát hiện nếu không có thiết bị đo chuyên dụng. Nếu túi nilon thành phẩm được sử dụng để chịu tải trọng lớn, hàng hóa sẽ có nguy cơ chịu nhiều rủi ro. Cũng giống như trong một đường ống nước, điểm mỏng nhất sẽ chịu áp lực lớn hơn những điểm còn lại và có xu hướng bị phá vỡ khi áp suất vượt quá mức cho phép.
Ngược lại, khi điểm mờ nằm thấp hơn vị trí mà bong bóng bắt đầu được thổi phồng, nghĩa là màng sẽ bị kéo căng khi đã nguội đi và các liên kết phân tử nhựa đã được định hình xong. Việc kéo căng này sẽ không còn mấy ý nghĩa, màng sẽ có xu hướng dày và chai sạn hơn, mất đi độ linh hoạt và mềm dẻo cần có.
Để khắc phục tình trạng này, trên lý thuyết chỉ cần đơn giản chỉ cần tăng hay giảm tốc độ đẩy nhựa ra của trục đùn. Tuy nhiên trên thực tế, việc thay đổi tốc độ này lại làm thay đổi tỷ lệ lực kéo. Đồng thời, việc nhựa được đẩy ra nhanh hay chậm hơn cũng làm thay đổi thời gian chúng được tiếp xúc với nhiệt độ trong trục đùn và việc nung chảy nhựa có thể sẽ không đạt được hiệu quả.

3. Sản phẩm túi nhựa LDPE như thế nào là đạt tiêu chuẩn?
a. Những yêu cầu về mặt hình thức bên ngoài của túi nhựa LDPE
Với đặc tính nổi trội của vật liệu là dẻo dai và linh hoạt, màng polyetylen sản xuất ra được coi là đủ tiêu chuẩn phải giữ nguyên được đặc tính trên. Bề mặt màng phải phẳng và nhẵn, không nhăn nhúm và không được có những đường gân gồ ghề hay những hạt nhựa sần sùi. Những nếp gấp sống hình thành do màng cán qua trục lăn không đều, có thể được chấp nhận.
Bao bì đạt tiêu chuẩn cũng không được phép có bọt khí, lỗ thủng và các vết rách, không có đốm đen, tạp chất và bị nhiễm bẩn.
b. Kích thước và độ sai lệch cho phép đối với bao bì nhựa LDPE
Nếu chưa từng trông thấy quy trình sản xuất bao bì nhựa, chắc hẳn sẽ có nhiều người nghĩ rằng các loại túi nhựa sẽ được đúc từng cái bằng khuôn. Vì thế khi đặt mua mặt hàng này, nhiều người đưa ra yêu cầu các thông số chiều dài và chiều rộng, độ dày đều phải tuyệt đối chính xác đến từng micromet.
Nhưng trên thực tế, độ dày cũng như chiều ngang của màng được quyết định bởi sự điều chỉnh kết hợp của rất nhiều yếu tố như: nhiệt độ, lưu lượng khí nén bơm vào, tốc độ của trục đùn và con lăn kéo màng. Sau khi khởi động máy, công nhân vận hành sẽ canh chỉnh các thông số trên cho tới khi cuộn nilon thu được đạt được kích thước như theo yêu cầu. Phần màng nhựa thu được trong lúc người công nhân vẫn đang trong giai đoạn điều chỉnh các thông số đương nhiên sẽ có kích thước sai lệch, và sẽ được đưa vào kho phế liệu.
Thế nhưng trong khi vận hành, nhiều yếu tố có tác động rất nhỏ như: một lượng nhỏ tạp chất trong nguồn nguyên liệu, cường độ của điện lưới bị thay đổi, hay áp suất khí nén trong màng bị giảm do thẩm thấu, hay một cơn gió mạnh lọt vào khu vực sản xuất cũng có thể làm cho các thông số của màng bị sai lệch. Vì vậy trong quá trình sản xuất, công nhân vận hành máy phải liên tục đo đạc và kiểm tra kích thước bao bì để điều chỉnh lại những sai lệch nếu có.
Do có quá nhiều yếu tố có thể tác động đến chất lượng sản phẩm, và quy trình sản xuất có thể bao gồm một loạt các tác vụ thủ công, nên kích thước và độ dày của bao bì nhựa không thể có trị số tuyệt đối. Mức sai số được cho phép trên bao bì thành phẩm thường ở mức dưới 3% cho kích thước và 5% cho độ dày. Nghĩa là khi khách hàng đặt hàng kích thước 100 x 200 cm với độ dày 100 micromet, một chiếc túi nhựa cỡ lớn 97 x 200 cm dày 95 micromet vẫn có thể được chấp nhận.
c. Đặc tính kỹ thuật và vật lý của túi
Các đặc tính bao gồm sức căng bề mặt và độ bền kéo.
Độ căng của bề mặt quyết định giá trị về khả năng được in ấn của màng. Để làm cho mực in hoặc keo composite có khả năng thấm ướt và bám dính tốt trên bề mặt màng polyetylen, sức căng bề mặt của màng phải đạt đến một tiêu chuẩn nhất định. Với chỉ số sức căng bề mặt quá thấp, mực sẽ khó bám dính tốt và dễ bị phai màu.
Đối với loại bao bì sẽ được in ấn, thông số này phải đạt tối thiểu là 38 dyne trở lên. Trên 40 dyne được cho là con số lý tưởng.
Sức căng bề mặt có thể được cải thiện bằng quy trình xử lý corona và plasma trước khi cuộn được quấn vào ống lõi.
Để đo được chính xác sức căng bề mặt của túi hoặc màng nhựa, cần có thiết bị đo chuyên dụng. Tuy nhiên có một cách đơn giản hơn được khá nhiều người áp dụng, đó là dùng mực để in thử lên sản phẩm bao bì, mức độ bám dính càng cao thì sức căng bề mặt càng lớn.
Độ bền kéo đại diện cho khả năng chịu đựng tải trọng và lực tác động bên ngoài của bao bì, một chiếc túi kém chất lượng sẽ nhanh chóng bị xé rách chỉ với một lực tác động vừa phải. Và việc thử xé rách túi này cũng là phương pháp đơn giản để thử độ bền kéo được nhiều người sử dụng nhất mà không cần tới các thiết bị chuyên dụng.
Độ bền kéo có được khi nguồn nguyên vật liệu là tinh khiết, không bị pha tạp, kết hợp với một quy trình sản xuất được thực hiện chuẩn xác.
Với các loại bao bì phải chịu tải trọng cực lớn, các chất phụ gia tăng cường độ dẻo dai và sức bền kéo cho màng sẽ được sử dụng.
4. Những lỗi thường gặp khi sản xuất túi nhựa LDPE, nguyên nhân và cách khắc phục
a. Độ dày của màng quá dày
Nguyên nhân:
- Độ dày quá lớn của màng LDPE có thể do khe hở đầu khuôn hoặc tốc độ của khuôn đùn quá lớn khiến nhựa bị đẩy ra quá nhanh.
- Điểm mờ quá thấp, màng được kéo căng khi đã định hình, khiến việc kéo mỏng màng kém hiệu quả.
- Lượng không khí làm mát trên đầu khuôn quá mạnh, làm mát phim quá nhanh.
- Tốc độ kéo màng lên của trục lăn quá chậm.
Giải pháp khắc phục:
- Điều chỉnh khe hở của đầu khuôn thổi.
- Giảm thể tích không khí của vòng khí làm mát. Thay đổi tỷ lệ lực kéo bằng cách tăng tốc độ kéo lên và giảm tốc độ trục đùn.
b. Độ dày của màng quá mỏng
Nguyên nhân:
- Khoảng cách khe hở trên đầu khuôn thổi quá nhỏ hoặc bị bám bẩn dẫn đến nguyên liệu nhựa đùn ra không đủ.
- Lưu lượng không khí của vòng không khí làm mát thấp, quá trình làm mát chậm. Màng ở nhiệt độ cao sẽ phải chịu lực tác động của con lăn kéo nhiều hơn khi chúng đã được làm nguội.
- Cũng có khả năng tốc độ của trục con lăn kéo quá nhanh, màng bị kéo căng quá mức.
Giải pháp khắc phục:
- Điều chỉnh khe hở của khuôn, vệ sinh nếu chúng bị bám bẩn.
- Tìm cách tăng hiệu suất làm mát và thử giảm tốc độ của trục lăn kéo.
c. Cuộn màng LDPE thành phẩm có độ trong suốt kém
Nguyên nhân:
- Chất lượng hạt nhựa không tốt, độ ẩm trong nguyên liệu quá lớn, hoặc nhiệt độ trong trục đùn thấp hơn mức cần thiết.
- Tốc độ kéo lên quá nhanh khiến cho cuộn phim không đủ thời gian được làm mát.
Giải pháp khắc phục
- Tăng nhiệt độ đùn thích hợp để nhựa có được sự nóng chảy đồng nhất.
- Kiểm tra lại nguồn nguyên liệu, phơi hoặc sấy khô nếu thấy chúng có dấu hiệu bị ẩm ướt.
- Giảm tốc độ trục lăn kéo lên hoặc bổ sung lượng không khí làm mát.
d. Màng nhựa bị nhăn nhúm
Nguyên nhân:
- Độ dày màng không đều, khi bị ép dẹp lại qua trục lăn kéo lên, điểm dày hơn sẽ có xu hướng được ép qua trục chậm hơn.
- Hiệu quả làm mát không đủ.
- Tỷ lệ thổi lên vượt quá mức cho phép, bong bóng màng quá lớn mà phần chân quá nhỏ sẽ mất trọng tâm và không ổn định. Bong bóng sẽ dao động qua lại giống như bị gió thổi, và màng cũng sẽ dễ bị nhăn. Không loại trừ trường hợp khu vực sản xuất có gió mạnh cũng dẫn đến hiện tượng này.
- Nẹp xương cá là 2 khung kim loại với nhiều con lăn với nhiệm vụ dẫn hướng bong bóng nhựa đi vào trục lăn kéo lên một cách chính xác. Nẹp xương cá trên máy thổi túi có hình dạng giống với mái nhà, nhưng cách thức hoặt động thì giống như một chiếc phễu úp ngược. Góc của nẹp xương cá phải phù hợp, nếu góc này quá lớn thì bong bóng nhựa sẽ bị ép dẹp lại trong một hành trình quá ngắn. Điều này cũng là nguyên nhân dẫn đến sự nhăn nhúm của màng.
- Áp lực hai bên của trục lăn kéo không nhất quán, một bên có tốc độ quay thấp hơn bên còn lại.
- Các con lăn dẫn hướng nằm rải rác nhiều vị trí trên hệ thống máy để tăng chiều dài hành trình của màng trước khi được quấn vào ống lõi. Nếu chúng không được đặt song song, cũng sẽ ảnh hưởng đến độ ổn định và độ phẳng của màng.
Giải pháp khắc phục:
- Điều chỉnh lại các thông số trên máy để màng có độ dày đồng đều.
- Cải thiện hiệu quả làm mát, cả trên hệ thống vòng khí làm mát lẫn môi trường trong khu vực sản xuất.
- Giảm tỷ lệ thổi lên, kiểm tra lại góc nẹp xương cá
- Điều chỉnh tốc độ vòng quay motor của trục lăn kéo lên cho đồng đều cả 2 bên. Nếu hệ thống của bạn chỉ sử dụng một motor cho trục lăn này, hãy kiểm tra và thay thế loại bạc đạn có chất lượng tốt nhất.
- Kiểm tra xem trục của các con lăn dẫn hướng có thật sự được đặt song song với nhau hay không.
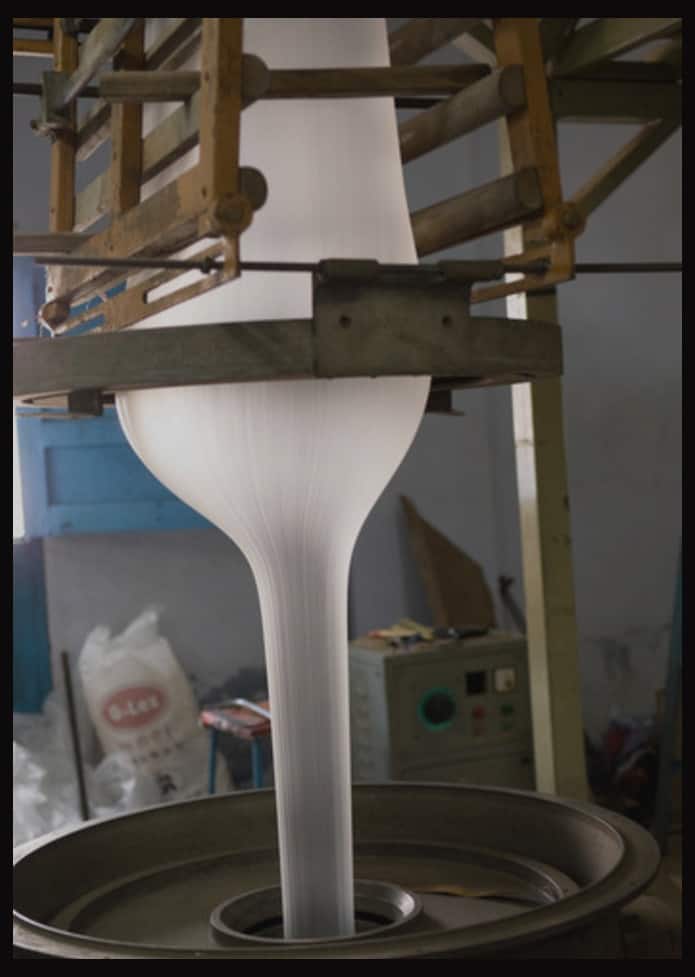
e. Cuộn màng có những đường vân mờ ảo
Nguyên nhân:
- Nhiệt độ đùn thấp hoặc chất lượng hạt nhựa kém, có độ ẩm cao.
Giải pháp khắc phục:
- Kiểm tra chất lượng hạt nhựa, làm khô chúng nếu hàm lượng nước vượt quá 0,3%. Tăng nhiệt độ trong trục đùn.
f. Bề mặt của màng gồ ghề không bằng phẳng
Nguyên nhân:
- Nhiệt độ đùn quá thấp khiến nhựa không được nung chảy hết.
- Tốc độ đẩy nhựa ra của trục đùn quá nhanh.
Giải pháp khắc phục:
- Cài đặt lại nhiệt độ nung chảy, giảm tốc độ đẩy nhựa ra của trục vít trên hệ thống đùn.
g. Độ bền kéo của màng kém
Nguyên nhân:
- Nguyên liệu kém chất lượng hoặc bị pha tạp, không đồng nhất.
- Nhiệt độ của nhựa nóng chảy quá cao cũng sẽ làm giảm độ bền kéo của màng;
- Tốc độ kéo lên theo phương thẳng đứng của trục lăn quá chậm khiến các phân tử nhựa được định hướng dọc kém hơn so với định hướng ngang gây mất tương xứng.
- Tỷ lệ thổi lên quá nhỏ thì lại làm giảm sự định hướng của nhựa theo hướng ngang, màng sẽ bị xơ hóa theo chiều này. Tỷ lệ thổi lên và tỷ lệ kéo phải phù hợp với nhau một cách chính xác, sao cho các phân tử nhựa được kéo giãn đều nhau ở cả hai phương ngang và dọc, mới khiến cho sản phẩm có được độ bền kéo tốt nhất.
Giải pháp khắc phục:
- Kiểm tra chất lượng nguyên liệu đầu vào, điều chỉnh nhiệt độ của trục đùn cho phù hợp.
- Tăng giảm một cách khéo léo tỷ lệ thổi và tỷ lệ lực kéo một cách khéo léo. Có thể cân nhắc thay đổi đầu khuôn thổi có kích thước phù hợp hơn.
h. Độ dày của màng không đồng đều
Nguyên nhân:
- Độ đồng đều khe hở trong đầu khuôn thổi ảnh hưởng trực tiếp đến sự đồng đều độ dày của màng. Nếu một điểm trên đầu khuôn có độ hở thấp hơn những vị trí khác, lượng nhựa đùn qua điểm này sẽ thấp hơn. Kết quả là trên suốt chiều dài cuộn màng nilon của bạn, sẽ luôn có một điểm mỏng hơn những chỗ khác.
- Sự phân bố nhiệt độ của đầu khuôn và trục đùn không đồng đều, dẫn đến có những vị trí nhựa chưa tan chảy hết, và có những chỗ thì nhựa lại bị nung chảy quá mức.
- Lưu lượng không khí xung quanh vòng khí làm mát không nhất quán, dẫn đến hiệu quả làm mát không đồng đều.
- Tỷ lệ thổi lên và tỷ lệ lực kéo được điều chỉnh chưa phù hợp.
- Tốc độ của trục lăn kéo lên không cố định và thay đổi liên tục. Khi chúng chạy nhanh hơn, màng của bạn sẽ bị mỏng đi và ngược lại.
Giải pháp khắc phục:
- Khe hở của đầu khuôn thổi không đều có thể là do bị bám bẩn, hãy vệ sinh chúng định kỳ mỗi tuần bằng hóa chất tẩy rửa chuyên dụng. Đặc biệt là sau khi máy ngừng hoạt động, nhựa nóng chảy bị khô lại sẽ dính chặt trong các khe hở trên đầu khuôn thổi.
- Đo lại nhiệt độ tại nhiều điểm trên đầu khuôn và trục đùn. Điều chỉnh lại nếu chúng chưa đồng nhất.
- Điều chỉnh, vệ sinh lại đường ống thiết bị làm mát để đảm bảo lưu lượng không khí đồng đều tại mọi cửa gió ra.
- Điều chỉnh tỷ lệ thổi lên và tỷ lệ lực kéo cho phù hợp.
- Đo lại tốc độ vòng quay của trục lăn kéo lên xem chúng có ổn định và bằng nhau ở cả hai bên hay không. Nếu tốc độ bị thay đổi, kiểm tra lại dây curoa truyền động hoặc biến tần của motor. Nếu tuổi thọ của máy đã quá lâu, có thể cần phải thay thế cả cụm thiết bị.
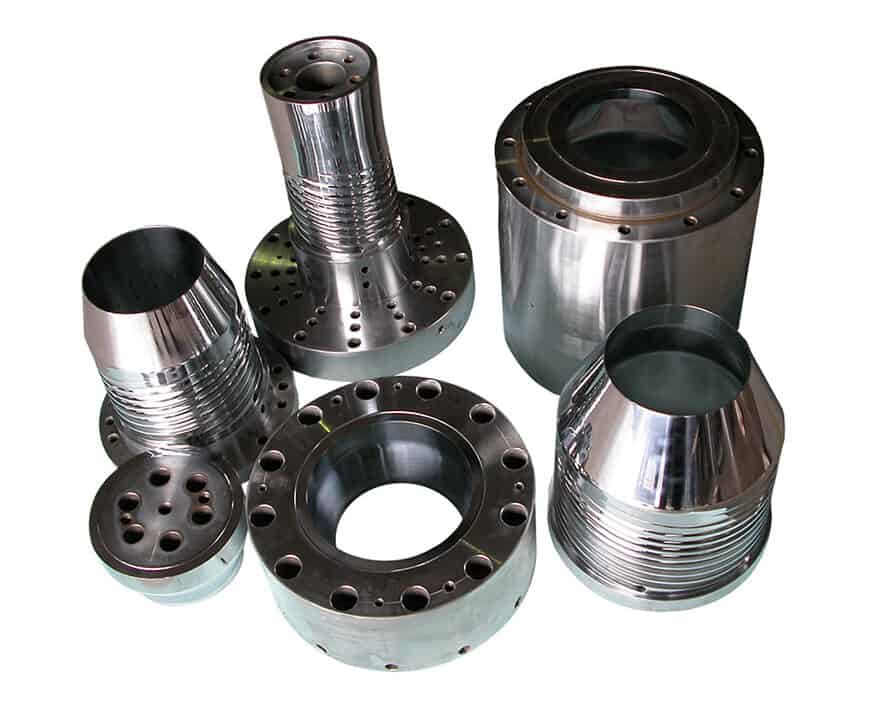
i. Hai mặt của cuộn nilon không dính khi ép nhiệt hàn đáy
Nguyên nhân:
- Điểm mờ quá thấp, các phân tử polyme được kéo giãn khi đã nguội, cuộn màng sẽ có hiệu suất giống loại màng nhựa được định hướng phân tử (như OPP), dẫn đến làm giảm hiệu suất hàn nhiệt.
- Việc bắt đầu bơm phồng và kéo giãn lớp màng nhựa đúng thời điểm vô cùng quan trọng. Thực hiện điều này khi nhựa đang ở trạng thái nóng chảy, tức là chúng ta đơn giản chỉ là định hình lại chúng, thành hình dạng mà chúng ta mong muốn. Thực hiện việc kéo giãn chúng khi đã nguội, chúng ta đang cố thay đổi và định hướng lại các liên kết phân tử trong chúng. Sau quá trình này, nhựa đã ở trạng thái bền vững, khiến cho chúng khó kết dính lại với nhau hơn khi trải qua ép nhiệt.
- Tỷ lệ giãn nở và tỷ lệ lực kéo đều ở mức quá lớn cũng phá vỡ các liên kết phân tử, ảnh hưởng đến hiệu suất niêm phong nhiệt của cuộn màng.
Giải pháp khắc phục:
- Điều chỉnh thể tích không khí trong vòng khí làm mát để làm cho điểm sương cao hơn một chút.
- Không cố gắng sản xuất loại túi nilon có kích thước lớn với một đầu khuôn và trục đùn được thiết kế cho kích cỡ nhỏ hơn. Việc này dẫn đến tỷ lệ giãn nở luôn ở mức cao, dẫn đến việc phải thay đổi tỷ lệ lực kéo, tốc độ trục đùn và nhiều thông số khác. Kết quả là một quy trình sản xuất khó kiểm soát và sản phẩm thu được không đủ tiêu chuẩn xuất xưởng.
j. Bong bóng khi thổi màng không ổn định
Nguyên nhân:
- Nhiệt độ đùn quá cao khiến việc làm mát kém hiệu quả, nhựa nóng chảy có độ dao động lớn khiến cho bong bóng màng kém ổn định.
- Tốc độ của trục đùn quá thấp khiến bong bóng màng không đủ nguồn cấp nguyên liệu để tạo hình. Chúng trở nên méo mó và dễ bị dao động.
- Khối lượng không khí của vòng khí làm mát không ổn định và đồng đều ở mọi cửa gió.
- Bị nhiễu động và ảnh hưởng bởi các luồng gió mạnh từ môi trường bên ngoài.
Giải pháp khắc phục:
- Điều chỉnh nhiệt độ và tốc độ trục đùn, kiểm tra lại hệ thống làm mát.
- Ngăn chặn và giảm thiểu sự tác động của các luồng không khí thổi qua khu vực sản xuất.
k. Màng quá dính và túi nilon thành phẩm khó mở miệng
Nguyên nhân:
- Công tác thu mua vật liệu thô đã có sai sót. Có thể chúng không phải là hạt nhựa polyetylen mật độ thấp cấp độ màng thổi, không có chất chống bám dính hoặc có nhưng hàm lượng quá thấp.
- Nhiệt độ của nhựa nóng chảy quá cao và sự không ổn định của bong bóng màng cũng dẫn đến hiện tượng trên.
- Tốc độ làm nguội quá chậm, màng vẫn còn nóng khi đi qua con lăn kéo, và bị dính vào nhau dưới áp lực của 2 trục lăn này.
- Tốc độ của trục lăn kéo lên quá nhanh cũng có thể cho màng bị dính chặt vào nhau, nhưng với một xác suất thấp hơn những nguyên nhân còn lại.
Giải pháp khắc phục:
- Kiểm tra và thay thế vật liệu nhựa cho phù hợp. Bổ sung chất phụ gia giúp màng trơn trượt và dễ mở miệng hơn có thể được sử dụng như một giải pháp tức thời.
- Giảm nhiệt độ đùn và tăng lưu lượng khí làm mát một cách thích hợp.
- Thử làm chậm tốc độ của trục lăn kéo.
Ở những nhà máy có tiêu chuẩn xuất xưởng nghiêm ngặt, sản phẩm túi nhựa chỉ cần mắc một trong những lỗi kể trên đều sẽ bị coi là không đạt. Chúng sẽ được đưa vào kho phế liệu để chờ được đưa đi tái chế.
Và những sai sót này chưa phải là tất cả, sản phẩm túi nhựa có thể còn trải qua các công đoạn gia công khác như: in ấn, dập quai, đục lỗ, tạo gân để trở thành túi zip, hay cắt seal để trở thành túi dán miệng.
Mỗi quy trình gia công này lại có những hệ thống máy móc và những thông số kỹ thuật riêng, cùng với vô vàn những trục trặc khác có thể gặp phải. Thật đáng tiếc vì trong phạm vi bài viết này, chúng tôi chưa thể truyền tải tất cả những thông tin đó tới độc giả, bởi vì chúng cũng đều là những câu chuyện dài!